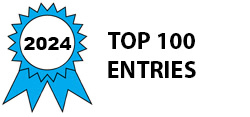
Innovation:
A team from Caltech, JPL and Dow have designed an autonomous, quadruped, climbing robot that can inspect the interior of complex chemical plant equipment. The motivation is for a safer alternative to human entry into confined spaces. The target application is inside distillation columns which can be over 200 feet tall and consist of a series of complex trays. The surface of each tray is covered with small valves, downcomers, and manway holes for climbing access. The column interior is very dark and often dirty with fouling. Such environments are highly difficult to navigate by humans and even robots.
Existing, out-of-the-box quadruped robots are not made for rigorous climbing. After 5 years of intense R&D, this team developed a first-of-its-kind robot that does. One of several innovations was adding a roller arm mounted on the back of the robot. The arm pivots front-to-back, and the roller wheels extend and contract laterally to support the robot’s weight as it climbs through the manway holes from tray to tray. Cameras mounted on the robot enable perception algorithms to detect column features and to determine the robot’s relative position. The cameras also provide high resolution visual inspection data to a human operator located safely outside of the column. Given the space constraints, the robot cannot carry its own power supply, so is tethered. A tether pod holds two spools of cable and descends through the column in sync with the robot during an inspection mission. One end of the cable is attached to the top of the column, the other to the robot. The tether pod actively spools the cable and provides enough tension to prevent the robot from tripping on it.
Feasibility/Manufacturability:
The initial prototype of the inspection robot was built on a commercially available quadruped and tested on a mock column setup. The roller arm and tether pod were custom built and securely attached. Custom software for perception, localization, and safety-critical control was developed to enable the quadruped to navigate the confined area. Functionality beyond basic visual inspection is anticipated in future iterations. For example, mounting instruments on the roller arm for more “hands-on” testing or adding hooks to the robot’s feet to interact with manway hole covers.
Marketability:
Distillation columns are a workhorse operation in many industries, from refining to distilling. All of these columns require periodic inspection to ensure their mechanical integrity. Currently, this task is done by humans with all the risks from being inside a confined space. Asset owners are seeking non-human alternatives, and not just for distillation columns, but also tanks, vessels, large pipelines, etc.
The current alternatives are deficient. Camera systems lack the ability to view behind obstacles and are not extendable for more “hands-on” inspections. Small aerial drones are too challenging to navigate in tight spaces and also are limited to only visual inspection.
Dow, a co-developer and owner of many distillation columns, will be the early adopter of this and other technologies to reduce confined space entries for the broader industry.
-
Awards
-
2024 Top 100 Entries
Like this entry?
-
About the Entrant
- Name:Ryan Eggebrecht
- Type of entry:teamTeam members:
- Aaron Ames
- Jaemin Lee
- Jeeseop Kim
- Wyatt Ubellacker
- Arash Kalantari
- Katherine Tighe
- Twain Pigott
- Marty Robinson
- William Rifenburgh
- Ryan Eggebrecht
- Patent status:pending