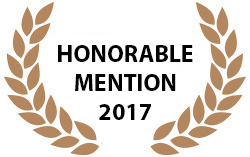
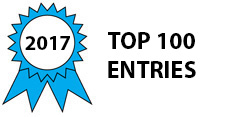
Reaction wheels (RWs) are not only the standard solution for attitude control of conventional spacecraft such as telecommunication satellites, but they are also frequently used in smaller satellites with demanding attitude control requirements. Due to their simplicity and compactness, ball bearings are commonly utilized for mounting RWs, especially in smaller satellites. However, ball bearings have several disadvantages. For instance, mechanical friction and wear limit the reliability and lifetime. Moreover, RWs with ball bearings are usually operated in a hermetically sealed atmosphere for preventing the outgassing of the bearing lubricant, which adds to the weight, cost and the complexity of the system. Another disadvantage of ball bearings is their contribution to the microvibrations, which is a major problem in small satellites with missions requiring high positioning precision.
Magnetic bearings, due to their contactless operation and ability to work in vacuum, increase the lifetime and remove the need for hermetic sealing. Moreover, the microvibration signature can be significantly reduced and reshaped owing to the ability of rotating the RW arounds its center of mass, and controlling the force envelope actively. However, commercially available, standalone magnetic bearings are not suitable for small satellites due to their bulky sizes and additional system complexities such as additional sensor requirements.
Therefore, a magnetically levitated RW with an integrated electrical drive, magnetic bearings and sensors are developed in a collaboration of researchers from the Power Electronic Systems Laboratory of ETH Zurich and Celeroton, an ETH spin-off specializing in ultra-high-speed electrical drives. This complete integration allows for a very compact system. Due to the novel arrangement of the permanent magnets in the rotor, the same materials are utilized for both magnetic bearing and the rotational drive, resulting in an axially short rotor. This, in turn, allows for unprecedented ultra-high-speed operation of the RW. In a hardware demonstrator, the feasibility of 30 times higher speed (300 000 rpm) compared to state of the art (< 10 000 rpm) is demonstrated by measurements. Simply by operating at those speeds, the mass of a RW for a typical small satellite can be halved, as can be calculated by mechanical scaling laws.
The figures demonstrate the construction and the operating principle of the novel RW with integrated magnetic bearings. The RW’s position is controlled actively in all six degrees of freedom by different dedicated windings applying a torque, an axial force, and two radial forces on two sides of the RW. The rotor’s radial displacement is measured with micrometer-accuracy by two PCB-integrated eddy-current sensors on both axial ends of the machine.
The innovative arrangement of the electromagnetic parts and the integration of the RW directly into the electrical machine enables the application of today’s commercially successful high-speed drive technology into the fast growing market of small satellites, without the need of overcoming any major additional technological challenges in manufacturing, sensing or control. Therefore, today’s low-speed RWs utilizing ball bearings can be replaced by the new-generation ultra-high-speed RWs with minimum effort, especially in small satellites with stringent weight, volume and positioning precision requirements.
-
Awards
-
2017 Aerospace & Defense Honorable Mention
-
2017 Top 100 Entries
Like this entry?
-
About the Entrant
- Name:Arda Tuysuz
- Type of entry:individual
- Patent status:none