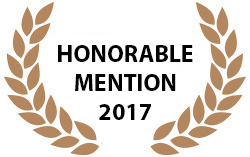
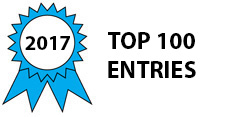
The patent pending engine design incorporates 12 sets of cylinders, each comprised of two opposing and one air pump (supercharger) piston, arranged radially in a rotating-cylinder cam-driven engine that uses diesel or JP-8 and completes 48 power strokes per revolution. Magnets are installed around the rotor periphery which, combined with coils in the radial housing, effect an integral motor/generator for starting, reverse, rapid acceleration, power generation, hybrid operation, and occasional silent running. Finally, the 12 vanes of a centrifugal cooling fan are incorporated between cylinders, and the fan’s intake air used to cool engine oil distributed via a centrifugal pump in the rotor body.
The breakthrough enabling construction of the efficiently packaged rotor was elimination of spark plugs or diesel fuel injectors via Homogeneous Charge Compression Ignition (HCCI). Timing uncertainty of HCCI is overcome using opposed-pistons with one driven rapidly toward the other as it begins its expansion stroke. Combustion occurs at any time after the process begins, and reverse torque produced at combustion by the rapid piston is ensured less than the forward torque of the expansion piston by specification of piston diameters, force angles, and lever lengths. The supercharger is regulated to elevate intake charge temperature nominally below autoignition temperature to minimize ignition delay and reduce the stroke and inertial loads associated with the rapidly moving piston. The supercharger is also oversized so intake conditions can be met during lean cold-start and operation at altitude. The upper load limit of HCCI is extended using many small bore steel pistons to handle HCCI combustion pressure at full load and push ringing frequencies beyond the audible range. Finally, the low load limit of HCCI is extended through idling of selected cylinders and excess compression preventing lean misfire.
Other innovations include use of hydrodynamic tilting pad followers in the outer cam tracks, enabling high speed operation under heavy load at low cost, and use of side ports feeding the in-cylinder ports of an opposed piston uniflow scavenged two-stroke, enabling independent management of intake and scavenge charges as well as continued expansion after the in-cylinder exhaust port opens.
Preliminary mechanical design and FEA were completed using Solidworks and analysis of thermodynamics, port flow, and performance evaluated in Excel using standard thermodynamics calculations and Hohenberg’s heat transfer coefficient. The engine/generator dimensions and weight are less than the engine/generator used on the RQ-7 but provide 3x the power density, 2.5x times the horsepower, and double the efficiency at sea level. Owing to the integral supercharger, power 1.5x the existing RQ-7 engine’s sea level performance is available at 15,000 feet. Constrained to low temperature combustion, the engine produces less power but with significantly fewer emissions making it well suited for scooters, lawn tractors, portable power generation, etc.
Development will continue in the next phase using standard tools (i.e. COMSOL, KIVA, etc.) augmented by critical experiments. A prototype will be constructed using a small 5-Axis CNC machining center then tested for FAA performance, endurance, and reliability.
-
Awards
-
2017 Aerospace & Defense Honorable Mention
-
2017 Top 100 Entries
Voting
-
ABOUT THE ENTRANT
- Name:Roderick Newstrom
- Type of entry:individual
- Profession:
- Number of times previously entering contest:1
- Roderick's favorite design and analysis tools:Excel, VBA, C#, Solidworks
- Roderick's hobbies and activities:Guitar, music, travel, hanging with my grandson.
- Roderick is inspired by:I am inspired by difficult problems and enjoy finding system solutions that balance all factors to yield an elegant and efficient design that is innovative and unique.
- Software used for this entry:Solidworks
- Patent status:pending