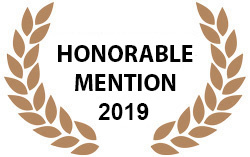
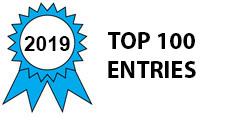
Carbon fibre reinforced polymer composites (CFRCs) possess properties that supersede their individual components and are being increasingly adopted in the aerospace industry. CFRCs have a complex structure that contributes to their unique properties but also makes them prone to an increased variety of damages such as fibre breakage, debonding, transverse-ply cracking, and delamination. Increasing the routes to potential failure with increased complexity of the failure mode is their major disadvantage. They require frequent visual inspections which has distinct disadvantages: 1. It is time consuming and tedious, 2. There is potential for mistakes and human error, 3. High cost for automated visual systems, 4.non-visibility of surface and subsurface damage that leads to low possibility of accurate visual inspections, 5. Inability to do this mid-flight or in-line.
Because of these disadvantages, they can fail unexpectedly and seriously. Combating this is a requirement for turning CFRCs into a robust material for widespread usage within and outside the aerospace industry.
Conventional non-destructive-testing techniques of damage detection include methods utilising ultrasound, thermography, radiography, and acoustic-emissions techniques. They exhibit reliable results and good sensitivity; however, these are all limited to specialised inspectors, tedious/onerous, have high time consumption, and a high cost of specialised equipment. It needs point testing. Magnetostrictive ribbons (these experience a change in magnetisation in response to an applied strain) are also an alternative as damage detection actuators. They however face issues with spatial sensitivity due to ‘hot spots’ appearing the closer they are to the ribbon. Another requirement is to demonstrate ease-of-fabrication in conjunction to damage detectability, and also to maintain a good weight-to-cost trade-off. The ribbons must be co-cured onto the composite surface and lack these properties.
An inexpensive alternative is proposed here and has been tested and demonstrated to meet surplus to these requirements. The two-part solution is to homogeneously embed dispersions of magnetostrictive microparticles within a suitably thin flexible matrix as an adhesive patch, which is then coupled to an adhesive sparse-array sensor grid that can be used to determine damage position and provide off-line measurement ability. Experimental testing has been combined with computational modelling and simulations to comprehensively study this approach. COMSOL simulations have shown that damage position can be detected in a two-axis sensor setup. Simulations have also shown that the strain experienced by magnetostrictive particles embedded in a softer material will be enhanced, supporting this idea. Taken in combination and brought to its logical conclusion, this approach can be used to cover critical components in the aircraft and used for off-line detection with near instantaneous updates possible.
The actuator is produced using inexpensive micron-sized particles of iron ferrite using epoxy polymers/curing agent for the embedding matrix. Similarly, sensor production has been prototyped by utilising copper induction coils: miniaturisation can be realised through inkjet printing. Production complexity arises from our solutions to the mixing and dispersion processes, and the strategies employed to ensure cost-effective sensor production.
The images demonstrate the fabricated prototype and the test results of the actuator and sensor; the product can be priced at £5/m^2
-
Awards
-
2019 Aerospace & Defense Honorable Mention
-
2019 Top 100 Entries
Like this entry?
-
About the Entrant
- Name:Zhaoyuan Leong
- Type of entry:teamTeam members:Zhaoyuan Leong, Nicola Morley, and Pratik Desai
- Patent status:none