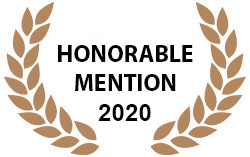
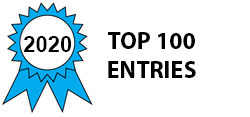
Currently all commercial continuously variable transmissions (CVT’s) in the automotive industry function on a friction drive principle. This friction drive interface exists between two hardened smooth steel surfaces separated by a traction fluid film. Traction fluid has the unique property in that it solidifies under high pressure, typically between 1 to 4 GPa, and then provides a traction coefficient of friction that varies from about 0.05 to 0.1. A number of factors determine the friction coefficient as well as the efficiency of the friction drive and as a result current commercial CVT’s do not feature high mechanical efficiencies, with a typical average mechanical efficiency of about 85%. Traction drive technology is a very well matured technology and has been in development since the 1980’s.
The RADIALcvt is a multi-parallel power path type of CVT that utilises traction drive technology in a novel mechanical configuration which optimises the factors contributing to high mechanical efficiencies in traction drives. The following fundamental advantages sets the RADIALcvt apart from current CVT’s in the automotive industry to present the RADIALcvt as a cost effective, high mechanical efficiency CVT.
One friction interface: Only one friction drive interface in series in a parallel power path. All other CVT’s, developmental and commercial have 2 friction drive interfaces in series thus resulting in a compound friction loss.
Line contact: The friction drive contact in the RADIALcvt friction drive can be a line contact, which is only possible in belt/chain CVT and cone ring CVT and not possible in toroidal and planet ball CVT’s. Line contact reduces the maximum contact stress.
Constant input radius: The RADIALcvt has a constant friction drive input radius. All other CVT have a variable input radius which results in high surface rolling speeds and lower coefficient of friction which require higher clamping forces.
Six parallel power paths: The RADIALcvt has at least 6 parallel power paths. Such a large number of parallel paths is only possible in planet ball CVT’s.
No hydraulic control: The RADIALcvt is realised without any hydraulic control. All current developmental and commercial CVT require a hydraulic control system which adds cost, weight and complexity.
During 2018 the first RADIALcvt prototype was manufactured and tested and peak transmission efficiency was above 90% and a paper was published in SAE (https://www.sae.org/publications/technical-papers/content/2019-01-5021/) detailing the simulation and test results.
During 2019 the first Second Generation RADIALcvt, which features a novel direct ratio shifting mechanism, simplifying the design and increasing efficiency, was manufactured and tested and peak transmission efficiency of 94.7% was recorded.
Current development includes the introduction of a pure mechanical loading cam controlling the clamping force based on torque.
The effect of this loading cam is simulated to drastically improve efficiency at partial loads.
The RADIALcvt is ideal for pure electric vehicles, hybrids and ICE vehicles as well as for industrial applications.
A RADIALcvt for automotive use featuring three synchronous modes with a ratio range of 9 is featured at https://www.youtube.com/watch?v=Ro-A2vUfW80
Video
-
Awards
-
2020 Automotive/Transportation Honorable Mention
-
2020 Top 100 Entries
Like this entry?
-
About the Entrant
- Name:Jan Naude
- Type of entry:individual
- Software used for this entry:SolidWorks and Matlab
- Patent status:pending