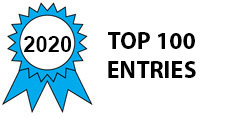
The Rotating Liner Engine is a design concept inspired by the WWII era Sleeve Valve Engines where the cylinder sleeve rotated and reciprocated in order to perform the valving on a 4 stroke engine (high BMEP aircraft engines). It was discovered that the rotation component of the motion minimizes engine piston ring friction and wear by extending hydrodynamic lubrication throughout the stroke of the engine. The RLE exploits this phenomenon by pure and continuous liner rotation, while leaves the conventional valving as is in order to preserve the environmental benefits of the modern engine design. The design has been refined so that conventional diesel engines can be converted to the concept. Estimate of fuel economy range from about 25% at idle to 4% at full load, and about 7% on the HD FTP (calculations published in SAE paper 2012-01-1963). However, based on current testing, these estimates may be conservative.
A four cylinder Cummins 4BT has been converted into a single cylinder RLE prototype (see pictures and video, details of design published in SAE paper 2012-01-1963). A similar baseline engine has been also prepared. Preliminary testing on the prototype have been published in SAE Paper 2019-01-0084. The results showed that the fuel economy at idle in the single cylinder is approximately 20% (which would translate into a 30% plus for a complete engine). However, more recent testing (to be published soon) show that the RLE is using about 30% less fuel than the baseline at 750 rpm idle (which may translate to over 40% for the complete engine). We have no test results under higher loads yet, but it appears that our prior friction models may have been conservative.
Conventional methods of improving fuel economy via friction reduction are limited to reducing oil viscosity and boosting the additive package to minimize the wear consequences. However, these methods yield very small results. From the literature, a 36 % reduction in viscosity can generate a 16% reduction in friction at low loads (margin reduces at high loads), at the expense of increased wear at high engine loads. This concept generates a higher friction reduction without changing lubricant viscosity, and the friction reduction margin should increase with load.
The design is relatively simple, and most existing engine platforms can be converted retaining the cylinder bore of the engine. The current prototype can easily be applied into a complete Cummins 4BT 3.9 or 6BT 5.9.
Video
-
Awards
-
2020 Top 100 Entries
Like this entry?
-
About the Entrant
- Name:Dimitrios Dardalis
- Type of entry:individual
- Software used for this entry:Multiple
- Patent status:patented