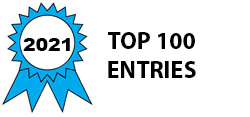
Reliability and endurance are of paramount importance for propeller driven aircraft. Electric motors are more reliable than internal combustion engines, yet also have new failure modes. The EnergySense aircraft propulsion system was created to address these new failure modes and increase endurance, or range, simultaneously. The novelty of the EnergySense system lies in the innovative application of streamlining the electric motor housing/heatsink while simplifying the entire propulsion system. For the emerging electric aircraft industry, this also means reduced component acquisition, installation and maintenance costs.
Most of the ground breaking work in the electrification of aviation still use off-the-shelf motors hidden under cowlings. Standard cooling air openings in cowling can account for five to fifteen percent of the total aircraft aerodynamic drag. Motor and motor controller cooling generally uses ancillary components such as coolant pumps, air fans, and some form of finned radiator as a heat exchanger. Each of these components add to the complexity of the system while reducing overall reliability and efficiency.
The patent pending EnergySense aircraft propulsion system consists of a streamlined motor and motor controller housing encapsulating the stator, rotor, controller electronics and pitch adjustor. The preferred motor topology is switched reluctance, which provides superior ruggedness, is insensitive to high temperatures and is over 90 percent efficient. This may not be as efficient as a permanent magnet machine, but there are no costly neodymium magnet to fail due to excessive temperature spikes. Switch reluctance motors (SRM) use very simple rotors with the stator windings embedded in the housing for maximum heat transfer. Recent advances in SRM rotor and stator designs and controller software means greater opportunities to refine this topology even more.
The streamlined housing of the EnergySense aircraft propulsion system is optimized for effective heat transfer from the SRM stator windings and the solid state power switches of the controller. The solid state switches are located adjacent to the stator windings, thus eliminating the use of heavy conductors normally found in segregated motors and controllers. The thermal mass of the housing is used to hold the transient heat generated during the initial ground roll of the aircraft where power is high and airspeed is low. The heat insensitivity of the SRM is also a safeguard against failure during this phase of operations.
The shape and surface finish of the housing has been engineered to maximize heat transfer while reducing aerodynamic drag. Continuing analysis is seeking to manage the laminar to turbulent airflow transition point to balance heat transfer and drag. While laminar airflow over the motor housing has less drag, it also has lower heat transfer than turbulent airflow. Examination of the Reynolds Number currently indicates the transition to be about half way along the length of the motor/controller housing.
The EnergySense aircraft propulsion system satisfies the industry’s requirements for a robust and efficient motor/controller unit for single and multi-engine light aircraft. Advanced system diagnostics along with increasing energy density of the batteries will complement this technology, creating the next major leap in air travel.
-
Awards
-
2021 Top 100 Entries
Like this entry?
-
About the Entrant
- Name:Carl Lawrence
- Type of entry:individual
- Software used for this entry:AutoDesk Inventor
- Patent status:pending