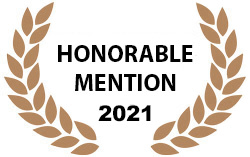
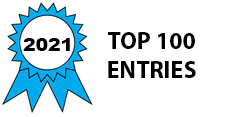
Full disclosure: this invention won the Aerospace and Defense category in 2017 for aviation applications, but this is a completely new application for the wind turbine industry.
Wind turbine operators have almost no direct knowledge of the aerodynamic state of their turbines’ airfoils. This has resulted in 36% underperformance and $12B in annual maintenance due to unanticipated failures (Sandia National Labs, 2017). Causes include icing, salt or insect contamination, airfoil erosion, and damage due to other environmental factors such as lighting strikes. Each of these can significantly degrade the performance of a wind turbine, but all are very difficult to identify, particularly on inaccessible offshore or remote wind farms. Current mitigation measures, such as continuous inspections, are expensive and primarily reactive, which limits their predictive value. As wind power is an integral component of every sustainable energy policy, and is growing at 10-25% annually, these losses are becoming ever more problematic, as the recent events following the recent Texas ice storm have highlighted.
The Enhanced Airfoil Performance Monitor (EAPM) is an electronic wind tuft that addresses these shortcomings by directly measuring the local airfoil “stress” on each turbine blade, as reflected by the turbulence intensity measured by EAPM. EAPM transmits local airfoil conditions wirelessly and in real-time to the turbine control station. The system can detect the smallest airflow perturbations, and can trigger alarms when certain threshold are exceeded. Further, the EAPM output can be used as a principal control element for the wind-turbine blade pitch. EAPM data is quantified and specific, and is therefore ideally amenable to Artificial Intelligence applications that further enhance the potential productivity gains achievable by EAPM.
The application of EAPM is best demonstrated by an example on a hypothetical off-shore wind-farm: one blade of a single wind-turbine of the hundred+ installed units is hit by lightning, resulting in some localized airfoil delamination. EAPM would instantly identify the affected turbine unit, blade, and even the segment of the affected blade. The operator could immediately dispatch inspection assets, such as a surveillance drone or a quick-response team, to address the issue before a potentially catastrophic failure occurs. Meanwhile, the existing “power curve” technology would barely detect the impact of the lighting strike, because it is buried by other factors such as salt contamination or routine blade erosion.
Without EAPM, the problem might not be identified until the next scheduled maintenance and inspection cycle, which could be months away. The turbine might fail catastrophically before then. Alternatively, frequent preventive inspections could be scheduled to preclude this situation, but these are expensive and wasteful, as each turbine must be shut down, perhaps unnecessarily, for inspection purposes.
EAPM has successfully completed Phase I testing with great success at the Nergica (Quebec) experimental wind turbine facility, and an 18-month Phase II test program is currently under way. EAPM is inexpensive and unobtrusive, and has the potential to markedly improve wind farm annual energy production, particularly in adverse circumstances, while significantly reducing both routine and unscheduled maintenance costs.
-
Awards
-
2021 Sustainable Technologies/Future Energy Honorable Mention
-
2021 Top 100 Entries
Like this entry?
-
About the Entrant
- Name:John Maris
- Type of entry:individual
- Software used for this entry:MATLAB
- Patent status:patented