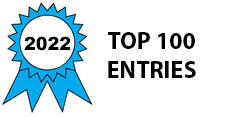
We have designed a modification for conventional diesel engines that provides a dramatic reduction of internal friction by rotating the cylinder liner. We have proven that a 300-600 rpm cylinder rotation (depending on engine size and operating condition) can eliminate the metal-to-metal contact environment between the piston rings and cylinder, as well as piston skirt and cylinder. The friction coefficient of the piston components for the high pressure parts of the cycle is reduced by up to 100 times. This more than compensates for the viscous friction added by the modest motion of the cylinder liner.
The challenge of course is the sealing mechanism between the cylinder head and the rotating liner. The seal needs to contain the gas with negligible leakage and no wear. We have designed a non-contacting hydrodynamic face seal that operates with very low friction and eliminates metallic contact. The rotating liner is supported by three journal bearings which have continuous oil flow. The conventional cooling jackets are retained, but the oil flow around the cylinder also contributes to the cylinder cooling. As a result to cylinder rotation, the peripheral thermal distribution and bore roundness is far better than conventional engines. The design details can be found in SAE paper 2012-01-1963. The prototype has been built by converting a four cylinder Cummins 3.9 into a single cylinder. The prototype has been extensively tested at idle (SAE paper 2021-01-0448) where the overall projected fuel economy benefit is of the order of 40 %. The prototype has been further tested under load. The video below is an example of such a test. These tests are currently in the process of publication. The test results show that the friction of the engine is substantially reduced as the load increases, which is the opposite trend to regular engines. The fuel economy benefit under load that corresponds to approximately 30 % of the maximum load of a heavy duty engine is about 12-14%. This level of friction reduction is of course substantially higher than what conventional lubricant and additives can offer.
The engine has been tested for over 100 hours so far under idle and medium loads. We have not tested the engine under higher loads yet, but we have confidence that the overall design is sound. The modification will fit most modern heavy duty engines, and the resulting fuel economy can be of the order of 10 %, depending on the load cycle. The life of the engine should also be considerably increased.
We plan to build a complete engine based on this single cylinder prototype. A complete Cummins 3.9 or 5.9 is a direct application of our current design, and this modification can potentially go into production with small changes.
Video
-
Awards
-
2022 Top 100 Entries
Like this entry?
-
About the Entrant
- Name:Dimitrios Dardalis
- Type of entry:individual
- Patent status:patented