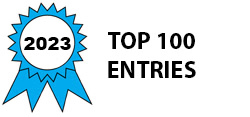
Global energy will shift predominantly to hydrogen and electric over the next 50 years with vital decarbonization benefits for our global environment. Advancing aviation’s future-state hydrogen and electric technologies is crucial to its sustainable future. NOVAdev’s mission is bringing those Earth Friendly Flight™ solutions to life.
EcoFlight™ EF-3K is NOVAdev’s zero-carbon air transport design for the 2030+ medium-range, single-aisle market – where 50% of aviation’s carbon dioxide emissions are generated. It is one of very few zero-carbon aircraft initiatives specifically designed for mainline commercial air service – meaning IFR 2,400 nm range, 150+ passenger capacity, and Mach .8 cruise.
The design was developed by a team of senior aviation engineering leaders having backgrounds with the industry’s most prominent commercial aircraft and systems manufacturers.
Importantly, EF-3K is conceived to ease FAA/EASA certification hurdles by pairing trusted technologies with innovative and safer “solid-state flux capacitor” hydrogen storage – patented NASA technology uniquely licensed by NOVAdev. It's realistic and certifiable approach to zero-carbon at airline scale is based on hydrogen fuel, turboelectric power generation, and distributed electric propulsion.
NOVAdev designed-in six foundational innovations destined to become standards in future zero-carbon mainline transports:
- Hydrogen Flux Capacitor™ storage – Based on patented NASA technology, it holds hydrogen in an “adsorbed” solid state, efficiently integrates with fuselage structures, and is safer and easier to certify than liquid hydrogen tanks.
- HITEP™ – NOVAdev's patented Hydrogen Intercooled Turboelectric Power unit is a first in airborne application of turbine intercooling and regeneration to markedly improve fuel efficiency. Five small HITEP™ units located in the tail and sponsons are networked and independently cycle off or on as power demand requires.
- Powered/Blown Wing – Electric propulsors mounted at the wing’s leading-edge centerline generates supplemental lift, improves aero efficiency, and reduces takeoff and landing lengths and speeds.
- Open Rotor Propulsion – Proven more efficient than ducted turbofans, EF-3K’s distributed propulsion enables the use of smaller rotors and eliminates noise associated with larger open rotor systems.
- Electric Ground Handling – Rotor propulsion is not required for ground handling as a battery powered nosewheel drive system auto-taxies and maneuvers the aircraft between gates and runways with GPS guidance, enhancing safety and relieving pilot and ground crew workload.
- Independent & Distributed Power Generation & Propulsion – Power generation and propulsion networks run independently, allowing their individual units to run at design point efficiency or be shut down to conserve fuel; far more efficient than two large turbofans predominantly running at inefficient power levels.
EcoFlight™ EF-3K takes advantage of highly matured turbine and electric systems, integrates them with new hydrogen storage technology in an innovative networked architecture and aerostructure, and captures the benefits of distributed power generation and distributed propulsion. System elements run at design-point efficiency, with power and propulsion elements flexibly optimized for take-off, cruise, landing or other flight regimes. The result is a high efficiency transport representative of zero-carbon, single-aisle aircraft platforms likely to emerge in the 2030 decade, making crucial contributions to global aviation’s decarbonization goals.
-
Awards
-
2023 Top 100 Entries
Like this entry?
-
About the Entrant
- Name:Michael Kramer
- Type of entry:teamTeam members:
- Richard Bartz
- Patent status:pending