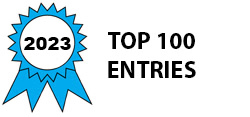
As industry and defense gradually shift to a modular space architecture, a reliable, autonomous process to assemble and integrate individual satellite modules in space needs to be developed. Due to the high cost of launching medium to large satellites, interest has developed for servicing and refueling satellites on-orbit. Enduralock’s team has designed the first satellite docking system that combines a mechanical connection, power or data transfer, and fluid transfer capability into one connector. FEA studies have been performed, and a prototype is in development.
The docking system consists of nested cones, which are CNC milled and are contained within sheet metal fabricated containers incorporated into the host and servicing satellites. The host satellite has a cone which is recessed and occupies 1-1.5u. There are numerous openings in the cone corresponding to electrical contacts, and a rotatory alignment feature is part of the rim of the cone. The host portion incorporates a rotatory actuator to cause recessed balls to engage and capture a pin groove on the service satellite’s cone. A linear actuator is utilized for undocking. The service satellite portion consists of a cone, which is initially retracted, and it incorporates a corresponding rotatory alignment feature. There are numerous openings in the service satellite’s cone corresponding to underlying pogo pin electrical contacts. The tip of the service satellite cone has a pin groove feature.
Before docking, the service satellite’s cone is extended. As the two satellites come together, the female rotatory actuator causes recessed balls to engage the pin groove accomplishing docking. The servicing satellite’s linear actuator then extends further to cause its electrical connectors to extend through the holes of the cones and engage their corresponding host electrical connectors. Torsional stability is accomplished by metallic blocks which extend through the two cones due to the action of the linear actuator. Once a hard dock is accomplished, fuel transfer down the central core of the cones occurs. Undocking is a reverse of the above steps, with the addition that the host satellite’s linear actuator, aided by a compression spring that is loaded during the docking process, accomplishes separation.
There are numerous benefits to the design. High value satellites can incorporate the host portion of the docking system. The service portion of the docking system can be incorporated into a 27u CubeSat or ESPA satellite, which would incorporate the customer’s electronics, power, or sensor upgrades and fuel. The servicing satellite would then be launched and would dock with the host satellite. The host satellite’s electronics and sensors would be upgraded, and it would be refueled extending its mission at a much-reduced cost to the launch of a new satellite. This process could be repeated with undocking and deorbiting of the first servicing satellite and docking of a new servicing satellite.
The design changes the economics of the CubeSat industry, with the mission life of CubeSats being extended. Linking multiple CubeSats in-space also multiplies their power and communications capabilities increasing their potential use for defense.
Video
-
Awards
-
2023 Top 100 Entries
Like this entry?
-
About the Entrant
- Name:Harold Hess
- Type of entry:teamTeam members:
- Zoltan Szekely
- Deeptesh Selvaraj
- Kishan Srinivas Indrani
- Caleb Grabill
- Jonathan Poulter
- Software used for this entry:SolidWorks, Abaqus
- Patent status:pending