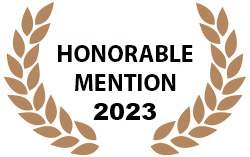
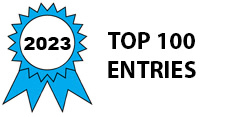
Excessive fan noise is prevalent everywhere, from noisy aircraft engines to annoying vacuum cleaners. The rise of drones or Unmanned Aerial Vehicles (UAVs) has contributed to this issue, particularly in cities, due to their constant humming. The incessant fan noise of drones can cause considerable nuisance and stress, contributing to noise pollution. This, in turn, can have potential health implications for inhabitants, affecting sleep and concentration.
Quieter drones and wind turbines are less likely to disturb wildlife, preserving natural habitats. Noise reduction can enhance user experience, boost public acceptance of drones, and facilitate their use in a wider array of applications. Hence, efforts to reduce drone noise are of paramount importance for a sustainable and harmonious co-existence.
To combat rising noise pollution, we looked to the concept of biomimicry. Owls are famed for their noiseless flight, a trait attributed to their specialized feather design. Each feather possesses three critical components: a velvety surface, comb-like leading edge hooks, and fringed trailing edges. Our AeroFeathers utilize these techniques to create airfoils that mimic the essential characteristics of owl feathers, promising less noise than contemporary fans.
While modern airfoil designs incorporate edge serrations, current manufacturing techniques fail to emulate all owl feather elements, particularly the fine fibers. Our recently published research showcases two innovative methods for 3D printing these thin fibers, enabling the inclusion of fibrous features akin to those of owl feathers to any solid structure.
As a target case, we look to incorporate our AeroFeather designs onto drone blades to reduce their noise. However, AeroFeathers can be implemented wherever fan noise is an issue. These include decreasing aeroacoustic noise in wind turbines, vacuum cleaners, computer server fans, and even restroom hand dryers.
AeroFeathers possess the potential to be of interest to both the business and consumer markets. Businesses whose products struggle with fan noise pollution, such as vacuum manufacturers, could use AeroFeathers to improve their commodities. Further, AeroFeather drone blades can be marketed directly to consumers, especially drone enthusiasts who wish to reduce their noise output.
By altering the 3D printing Gcode to create fibrous structures with tailored thickness and density, AeroFeather designs can be customized in many different ways. By using established Fused Deposition Modeling (FDM) 3D printing techniques, our designs can be fabricated using any low-cost commercially available FDM printer. Our designs can be manufactured using a variety of materials, from simple plastics to high performance metals. As a result, AeroFeathers can be repeatably fabricated at a low production cost, depending on the material used.
Video
-
Awards
-
2023 Aerospace & Defense Honorable Mention
-
2023 Top 100 Entries
Like this entry?
-
About the Entrant
- Name:William Johnston
- Type of entry:teamTeam members:
- Gabrielle Mathews
- Laura Nobles
- Maria Carrillo-Munoz
- Bhisham Sharma
- Software used for this entry:Matlab, ideaMaker, OpenSCAD
- Patent status:none