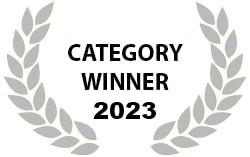
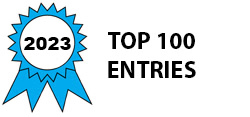
Operating revenue-generating assets in harsh environments poses safety and financial risks. For example, catastrophic wind turbine blade failures are costing $1.5 billion a year to fleet owners and operators across 700,000 blades in operation globally (Wind Power Engineering, 2018), and safety incidents have increased by 22.3% on wind farms (Global Offshore Wind Health and Safety Organization). Sensatek discovered that passive Radio Frequency-based (RF) wireless dynamic strain sensors are a promising technology to help safely watch assets used in harsh environments, such as trending crack growth on wind turbine blades to help eliminate 3,800 blade failures occurring annually (Engineering News Record).
The wireless RF vibratory strain sensors are passively powered, not requiring batteries, and are applied to the structure of interest by using a bonding method. A wireless gateway is installed nearby and is used to communicate with multiple wireless passive RF sensors and sends the data remotely to the cloud. The software application uses the data along with AI-deep learning to prioritize maintenance based on vibratory strain responses of the structure being monitored.
The passive RF vibratory strain sensor is based on a microstrip patch antenna that consists of a radiation patch, a dielectric substrate, and a ground plane. The microstrip patch antenna behaves as an antenna and a sensor whose frequency response depends on its geometry, whereas its ground plane contributes mainly to the response of the antenna sensor. As the structure experiences changes in strain stress, it causes a change in the radiation pattern of the microstrip patch antenna sensor. A miniaturized frequency-modulated continuous wave (FMCW) radar circuit is coupled with the sensor to enable dynamic interrogation of the antenna sensor enabling vibratory strain data to be generated based on the strain-stress profile of the structure the sensor is coupled to.
Competing methods such as drone inspections, wired strain gauges, acoustic monitoring, accelerometers, and vibration sensors are also used in structural monitoring applications. Those methods are expensive, results are often misdiagnosed, and require much maintenance to ensure the sensors are operational. Our solution is more effective because it monitors the damage more directly on parts such as wind turbine blades because sensors are installed in situ in hard-to-reach areas without requiring batteries or lengthy cables, further eliminating costs. Furthermore, our sensors provide information on the strain, vibration frequency, and load of the part being monitored, enabling a rich data stream that makes the AI-deep learning algorithm more robust to prioritize maintenance and safely mitigate catastrophic failures. In addition, they are manufactured for 5x less than the cost of competing solutions.
This technology has many applications besides wind turbines and includes airframes, gas turbines, space launch vehicles, electric machines, bridges, and natural gas pipelines, presenting a total global market opportunity of $11.6 billion (BCC Research) within the industrial, aerospace, and automotive markets. There is interest from companies such as GE, Lockheed Martin, Siemens Energy, Pratt & Whitney, and large utilities in piloting the technology.
-
Awards
-
2023 Electronics Category Winner
-
2023 Top 100 Entries
Like this entry?
-
About the Entrant
- Name:Reamonn Soto
- Type of entry:teamTeam members:
- Taofeek Orekan
- Azryana Soto
- Software used for this entry:Yes