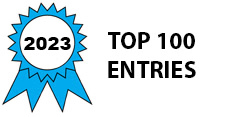
The Square Trajectory Mechanism performs the exact square trajectory, using only one source of rotational input and without any constraints or guidance applied to the output point of motion. The entire mechanical assembly is exclusively contained inside the square perimeter.
The kinematic design can be placed in the category of the exact-straight-line mechanisms (conversion of rotational motion into rectilinear motion), exhibiting the additional feature of performing exact-90-degrees-angles in the same time. There are neither interruptions nor changes in the directions of the rotating elements. Hence, the output point of motion traces the square path continuously and makes the transition from one side of the square to another instantaneously. The kinematic solution for using only one source of rotational input relies on a special shape periodic cam with two conjugated surfaces. The major break through of this design is the mathematical framework for which an unique equation determines the smoothness of the cam shape and a finite number of sinusoidal terms defines a perfect square wave function.
The features mentioned above (only one source of rotational input, unconstrained output and perimeter confinement) allow two identical mechanisms to be “mirror” connected on the output points of motion. The configuration of each of them consists of a square base frame and the inside perimeter mechanism. Operated synchronously , the two mechanisms produce an “orbiting” relative motion between the two square base frames, given the fact that none is considered stationary and the other mobile. In plain words, they go around each other. The most important characteristic of this behaviour is that the square base frames preserve orientation over the full 360 degrees of revolution, while maintaining the coincidence between either two sides or two vertices, alternatively. For the real application, the square base frames are converted into a rigid body comprising two opposing faces of a cube, connected by a central axle. This construction becomes a modular entity for a chain connection of multiple mechanisms. Using certain algorithms of permutations between modules, larger structures can be self-assembled, self-reconfigured, without any external action.
One of the aim of this type of modularity is adaptive architecture for harsh or inhospitable environments, where human presence is undesirable or additional construction equipment is prohibitive (Moon or Mars). Also, for space activity, deployment systems, from tightly packed configuration to the desired ones, are a primary condition for any orbit launch.
For a more tangible application, robotic reconfigurable buildings can be designed.. Depending on functional need, entire walls can be reconfigured, moved, assembled or disassembled. Future climate change may require smart buildings to posses adaptive behaviour.
Two proof of concept prototypes have been constructed and exhibited at international forums on robotics and modular robotics.
Detailed engineering on: https://www.raduapetroaia.com/
Video
-
Awards
-
2023 Top 100 Entries
Like this entry?
-
About the Entrant
- Name:Radu Apetroaia
- Type of entry:individual
- Software used for this entry:SolidWorks
- Patent status:none