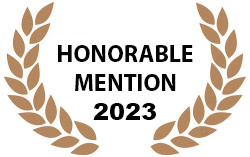
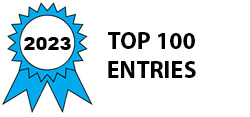
The quest for manufacturing green hydrogen fuel has gained increased urgency. Currently, the primary method of producing green hydrogen is electrolysis of water. As a water source, seawater offers many advantages over fresh-water, including its electrical conductivity much higher than that of fresh-water. Moreover, unlike fresh-water being considerably limited, seawater is an abundant natural resource on Earth. However, electrolysis of seawater (EOS) confronts an immense issue; the distinct kinetic advantage of Chlorine Evolving Reaction (CER) at the anode that overwhelms Oxygen Evolving Reaction (OER). As a result, high proportions of chlorine evolved at the anode rapidly proceed into byproducts (e.g., hypochlorous acid and hypochlorite ions) harmful to marine ecosystems.
The current state-of-the-art (i.e., the conventional approach) for suppressing CER and promoting OER is to apply coatings of catalytic chemical elements (CCEs) that promote OER on the anode. This conventional approach requires scant CCEs engineered through complex preparation procedures, implying that high-volume scaling would be very costly. Furthermore, this conventional approach limits the operational electrical current density Jc to less than 1 A/cm2, severely restricting the rate at which hydrogen is produced per unit time at the cathode (i.e., hydrogen production rate), which unavoidably drives the cost of resulting green hydrogen.
Our revolutionary approach showcases the following three distinctive features: (1) the use of Jc much larger (Jc>10 A/cm2) than that (Jc10 A/cm2 is a critical element that significantly suppresses CER and substantially increases the hydrogen production rate; (2) the use of consumable rod-shaped micro-electrodes with diameter ~1x10-3 m contrary to planar electrodes used in the conventional approach. A pair of rod-shaped micro-electrodes are placed face-to-face, restricting the conduction path through which electrical current flows, allowing the use of Jc >10 A/cm2 safely and continuously. The rod-shaped micro-electrodes are made of graphite that ranks most noble in the Galvanic Series, benefitting their endurance in the highly corrosive local environment at the anode. Furthermore, graphite being machinable, inexpensive, and abundant reduces material and manufacturing cost significantly in contrast to electrodes that employ costly CCEs in the conventional approach; and (3) the use of an array of rod-shaped micro-electrodes that is manufacturable through computerized-numerical-control (CNC) at cost economically acceptable in comparison to a pair of planar electrodes covered with pricey CCEs in the conventional approach. An array of rod-shaped micro-electrodes establishes strong electric-filed and desirable electric-field distribution that efficiently transport H+ and OH- ions produced at the anode and the cathode, respectively, to their respective counter electrodes, reducing acidity in the vicinity of the anode and suppressing CER.
In our small-scale demonstration, an EOS system equipped with a single pair of rod-shaped micro-electrodes was developed, which allowed EOS to be performed safely and continuously at Jc>10 A/cm2 and verified that CER was substantially diminished. A simple (i.e., highly scalable) EOS system that produces hydrogen at higher rates (i.e., an economic incentive) without generating toxic byproducts (i.e., an environmental incentive) is certainly a marketable product that will receive high demand.
-
Awards
-
2023 Sustainable Technology Honorable Mention
-
2023 Top 100 Entries
Like this entry?
-
About the Entrant
- Name:Nobuhiko Kobayashi
- Type of entry:teamTeam members:
- Søren Tornøe
- Software used for this entry:COMSOL
- Patent status:pending