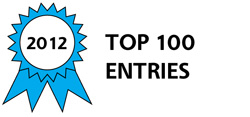
The goal was to design a highly accurate, cost effective dispense pump that would be 100% PTFE (Teflon) in the wetted flow path which results in excellent chemical resistance to acids and bases. PTFE also has extremely low surface energy which results in minimal retention for bio-pharma applications.
Traditional dispense pumps typically fall into two general categories that limit their capabilities in sensitive environments that cannot accept any degree of fluid leakage or contamination.
Syringe type dispense pumps have a linear output and reasonable pressure capability but they are not available in 100% inert materials due to the nature of their design which requires a dynamic seal to be in contact with the bore of the syringe. All dynamic seals have a small percentage of bypass (leakage) as the nature of their design. The level of bypass will increase over time due to wear. When dealing with highly caustic solutions, liquids that are hazardous or chemistries sensitive to atmospheric contact this becomes unacceptable. The particle generation resulting from dynamic seal wear is not acceptable in many industries such as semiconductor.
Diaphragm type dispense pumps resolve some of these issues but are typically limited in capacity due to the stroke capability of diaphragms. Diaphragms do not produce a linear volumetric output curve which limits their accuracy. The pressure capability is limited due to the unsupported nature of a diaphragm.
The pump that is being developed and tested overcomes these limitations. The patented design utilizes “rolling diaphragm” technology. The rolling diaphragm is supported between a cylindrical bore and internal support/actuator and is made from high purity PTFE. The fully supported nature of the design results in a high degree of stability in the structure which translates to a very accurate and repeatable volumetric dispense. Since the rolling diaphragm has no dynamic sealing surfaces there is no possibility of bypass (leakage). The lack of a dynamic seal and 100% PTFE flow path eliminates the possibility of particle generation and ionic contamination critical to sensitive industries such as semiconductor.
The rolling diaphragm and all wetted surfaces are constructed of PTFE which makes the pump inert to virtually all chemistries. The design has pressure capability in excess of 100 psi which allows injection into existing pressurized fluid streams or vessels. It also has the ability to self-prime. Due to the fully supported nature of the rolling diaphragm concept and linear characteristic of a cylindrical dispense chamber, accuracy has been an order of magnitude better than competitive products in testing. Initial tests indicate an accuracy of +/- 1/10th of one percent repeatability ( 0.1%) Competitive products typically advertise +/- 1 percent (1.0%). Due to the relatively simple nature of the design this is achieved at a projected price point which is lower than products currently available. The dispense pump only requires a regulated air source and in it’s current iteration is adjustable from 0 to 100 milliliter dispense volume per stroke. The design is readily scalable to support virtually any volumetric range desired.
Video
-
Awards
-
2012 Top 100 Entries
Like this entry?
-
About the Entrant
- Name:Kenji Kingsford
- Type of entry:individual
- Software used for this entry:SolidWorks
- Patent status:patented