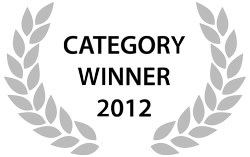
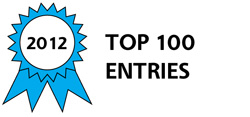
The thermal stir welding process (U.S. Patents 7,980,449 & 8,127,977) is a new solid-state (meaning the weld metal does not melt during welding) welding process invented at NASA's Marshall Space Flight Center. The unique welding process (FIGURE 1) decouples the heating, stirring and forging elements of friction stir welding and allows for the independent control of each element of the weld process. An induction coil first heats the weld joint material to a desired plasticized temperature, at which time, the weld joint material moves into a through-thickness stir rod that stirs the already plastic material. The stir rod can be independently controlled to rotate at a desired rotational speed, or RPM. Upper and lower non-rotating containment plates, also independently controlled, compress, or squeeze, the plastic weld zone to consolidate the plasticized material as it is being stirred. The stir rod protrudes through the center of the upper containment plate, through the weld material thickness, and is captured by the lower containment plate. One of the more important aspects of the weld process is the capability to weld at a specific temperature using closed-loop temperature control (patent pending). There is no other weld process capable of doing this. The closed-loop temperature control feature allows the operator to input a desired base-line temperature at which he wants to weld. An ultrasonic technology based temperature sensor monitors the internal temperature of the plasticized weld nugget, real-time, during welding. If the sensor senses the temperature increasing, it will relay the increased temperature to the controller, at which time, the controller will decrease the stir rod RPM, and/or, increase travel rate, and/or decrease induction coil power. These three events (either individually or in combination) will cool the temperature to the base-line temperature. Opposite action of the three events (i.e., spindle RPM, travel rate and induction power) will increase the temperature if the temperature begins to cool.
Another important aspect of the weld process is the capability to perform "angled" welds. Because the induction coil heats weld metal into a plastic condition, non-rotating containment plates can be shaped to accommodate weld joints of different geometries. For instance, the welding of flat plate material (FIGURE 2) obviously requires flat containment plates. The angled welds seen in FIGURE 3 require "angled" containment plates with a 120 degree angle. This allows the angled weld joint to be contained by the angled containment plates as the stir rod "stirs" the plasticized weld joint nugget material. Once again, stir rod protrudes through the center of the angled upper containment plate, through the weld material thickness, and is captured by the angled lower containment plate.
One of the most significant impacts on weld quality and strength is the temperature to which the weld nugget is subjected, especially in a solid state weld process. The ability to control welding temperature through the weld metal’s plastic regime will have a significant impact on overall weld quality.
-
Awards
-
2012 Machinery & Equipment Category Winner
-
2012 Top 100 Entries
Like this entry?
-
About the Entrant
- Name:Jeff Ding
- Type of entry:individual
- Patent status:patented