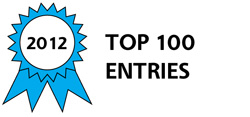
Radial Air Motor Based On Rolling Elements
The subject of this entry is a new type of positive displacement air motor or pump whose features include:
•Positive, variable displacement. Allows high-speed and torque with low air consumption and minimal loss of efficiency.
•Dynamically balanced. Allows higher rotational speeds than other positive displacement designs.
•Displacement can be adjusted during operation. Allows active torque changes in response to load, making this device both a motor and continuously variable transmission.
•Low parts count and simple internal geometries. Fosters manufacturability and reliability.
Our new design minimizes the speed, torque, efficiency and manufacturability tradeoffs that affect traditional air motors and pumps. Vane-type designs, for example, have speed limits and low efficiency because of the sliding friction inherent in their design. Gerotor types have extreme tolerance requirements and a high cost of manufacture.
Innovative Design, Familiar Components
The development of our air motor began with the idea that inexpensive bearing components could be transformed into a low-cost rotary air motor. Schematically, the motor resembles an inside-out radial piston aircraft engine, minus the crankshaft and connecting rods. The balls act as pistons in the rotor’s cylinders and roll inside an outer race as any rolling bearing would. However, this outer race is mounted eccentrically relative to the motor’s centerline. The pistons need not be spherical, and in fact are preferred to be cylindrical rollers running in rectangular cavities in the rotor.
Centerline eccentricity between outer race and cylinder block is what drives the motor: As the cylindrical pistons roll between the eccentric outer race and concentric cylinder block, the pistons move from top dead center position to bottom dead center cyclically.
Of technical interest is the high rotation rate of the pistons within their cylinders, and the friction force you’d expect on the cylinder walls in order to create torque. We have purposely made the prototype rotor of aluminum, so that we can readily observe the cylinder’s wear pattern. Theoretically, the wear pattern should be on the side of the cylinder, upstream of the piston in the direction of torque production. Our tests, however, show no wear in this region so far. A primary goal for some applications is for it to be running without lubrication. We theorize and intend that while running, a gas or hydrodynamic bearing develops within the motor at high speeds between the piston and cylinder wall, eliminating the primary wear concern.
Many Applications Possible
Originally, our air motor was designed for small air-driven grinding spindle for a developmental CNC mill that produces zirconia dental implants. As a developer of custom robotic and automation systems, our plans for this device have grown to include:
•Constant force counterbalancing of vertical loads
•High-speed air spindle drives
•High-efficiency air compressors
•Accurate fluid metering pumps and positive displacement flow meters
The architecture of our device extends well beyond robotics and machine tools. For example, we’re also investigating its use in vehicle drives for both unmanned aerial vehicles (UAV) and compressed air powered land vehicles.
Video
-
Awards
-
2012 Top 100 Entries
Like this entry?
-
About the Entrant
- Name:Michael Everman
- Type of entry:individual
- Software used for this entry:Solidworks, MS Excel, Autodesk Sketchbook Pro
- Patent status:none