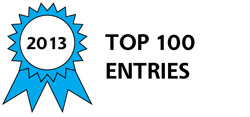
Remote manipulation in uncontrolled environments remains challenging despite advances in computing, robotics, and telecommunication. Complex objects can be manipulated with custom fixturing, but this limits adaptability in dynamic environments. Due to their ability to grip and manipulate objects with myriad shapes and textures, humans are still required to manufacture complex devices and structures in extreme environments (i.e. underwater, space, war-zones, etc). This ability is dependent not only on the orientation of the digital manipulators, but also on the ability to dynamically control the force applied to the manipulated object.
Fingers allow a variety of objects to be manipulated without damage. Attempts to mimic the physiology of the human hand result in simple forms with limited movement, adaptability, and performance. Attempts to mimic the anatomy of the human hand result in overly complex mechanics, high fabrication costs, and cumbersome control mechanisms. Recent advances in flexible robotics provide the means to mimic the dynamic adaptability of fingers with the stability and control mechanisms of robotics.
The dynamic performance capability of fingers can be separated into two components: axial stiffness and flexural modulus. High axial stiffness allows manipulated objects to be pushed, lifted, and secured without damaging the finger-like manipulators. High flexural modulus allows fingers to grip objects with irregular shapes, without causing damage, and with minimal object contact required. Epic Robotic’s Aerial Arm is composed of four hollow-core stainless steel braided shafts combined with plastics of varying compositions and durometers. The braid geometry and plastics selection results in controllable and dynamic bending points along the length of the Arm. The hybrid metal-plastic design allows tuneable performance as desired for all applications. Furthermore, Aerial Arm can be controlled manually, electrically, or robotically as needed. The fundamental technology behind Aerial Arm is low cost, but the level of control can range from simple mechanical connections to a robotically controlled system allowing for telepresence and remote manipulation.
Figure 1 shows the basic design of Aerial Arms and a proof of concept model complete with electrical motors and actuators. The Arms consist of a hollow braided shaft covered in plastic and fly-by-wire control mechanism. Figure 2 shows the Aerial Arm in a deployed state with the fingers in a slack position and showing the reach of flexible robotics. Figure 3 shows a close-up of the electronics package and an example of the Aerial Arm manipulating a racket ball. Aerial Arms weighs less than a pound and has synchronized motion allowing for precise control of the manipulators. Furthermore, the hollow shaft allows for the deployment of commercially available tools and devices to be used in conjunction with the mobile manipulator (i.e. a camera, gripper, or cutting device).
This device can be easily attached to a mobile platform (i.e. RC car, plane, or helicopter) and controlled remotely. Aerial Arms’ design has myriad applications including remote manipulation, prostheses, and extreme environment manufacturing.
-
Awards
-
2013 Top 100 Entries
Like this entry?
-
About the Entrant
- Name:Robert Tucker
- Type of entry:teamTeam members:Rob Tucker
Joe Bogusky - Software used for this entry:SolidWorks
- Patent status:pending