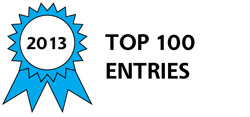
Wind power seems benign and safe, but there are several problems: bird/bat strikes, noise, vibration, large normal force at the tower top from blade lift, slow adaptation to wind direction changes (and correspondingly large blade stresses), etc. that are all solved here. My goal is to allow distributed wind power capture that is inherently safe and works from lighter winds than conventional turbines require, located close to each load to eliminate power distribution losses. This also provides improved energy security because without need for long power distribution lines the threat of blackout in storms from broken power-lines is eliminated. And, of course, this is completely carbon-free in operation.
The key is to align the lift force from all rotor blades to directly provide hub torque. This forces the rotor to turn slowly, dramatically increasing safety and eliminating the threat to flying animals. Rotor blades are oriented for low drag, now the only remaining normal tower-top force. Because this rotor turns very slowly it has small angular momentum, allowing it to rapidly adjust to wind direction changes. This rotor also serves as the pointing ‘tail’, further simplifying product design and cost. Noise is imperceptible because the tip speed is less than the wind speed, not 8 times higher as in normal wind turbines.
Blade cost is greatly reduced from the lower speeds and torque-aligned forces. Tower cost is also greatly reduced because there is no lift-force from the blade pushing back on the tower top. Therefore this can be placed on any pole or tower for local power. Or put one on every ‘phone pole’ in a city, and 100,000 generators at 10 kW each is 1000 mega-watts the city can use.
This design is fundamentally different from all wind turbines in commercial use. It seems that the aircraft propeller has motivated wind turbine design, but this is not optimal because the propeller is designed to provide a forward aerodynamic force from engine torque. This becomes a backwards force in the direction of the wind on conventional turbines, raising costs significantly without providing any benefit.
Manufacturability is easier because blade operating stresses are low, and there is no twist required along the blade. Control for high wind is passive (loaded springs) taking advantage of the airfoil pitching moment to naturally reduce angle of attack in high wind. No need for high-tech battery powered control systems to either operate this turbine, or to keep it safe. It therefore operates at any wind speed, maintaining power generation after all conventional wind turbines have shut down for protection.
Costs are low enough to consider using these widely in underserved areas.
-
Awards
-
2013 Top 100 Entries
Like this entry?
-
About the Entrant
- Name:Earl Mccune
- Type of entry:individual
- Software used for this entry:Matlab
- Patent status:pending