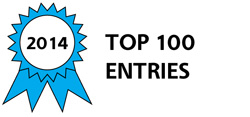
Future engines must meet tough fuel economy and emissions standards without sacrificing power. Variable valve actuation (VVA) can help, but current engines with VVA all have camshafts, so they are not fully variable. LIM Technology has invented a pneumatically actuated, digitally managed valve which is fully variable and requires no camshaft. The video shows how a LIM valve works in our 2-stroke engine, and how it might work in a 4-stroke engine.
Installing LIM valves in our optimized 2-stroke diesel offers the best combination of:
- fuel efficiency.
- power density.
- simplicity
- manufacturability.
Unlike some proposed “fully” variable systems, LIM valves are not limited by:
- electrical system capacity.
- mechanical complexity.
- magnetic saturation.
Compared to conventional valves, LIM valves:
- open, close faster (less mass = lower inertia, no spring resistance, no cam lobes to follow).
- can open and close at any crank angle.
- are digitally managed (by a PCM map).
- have longer, fully variable, dwell (can flow more air).
- reduce friction (no side load; no camshaft or related parts).
- can open and close independent of other valves (inducing turbulence).
- control ventilation more precisely for advanced combustion (RCCI, PPC, GCI).
LIM valves have been installed and tested in three proof-of-concept engines. We kept the 2-stroke’s uniflow design for its volumetric efficiency and efficient scavenging, but reversed it so air enters each cylinder through four LIM valves in the head, and exhaust exits through ports in the lower cylinder wall. With no camshaft, the engine is lighter and costs less. It has about 90% greater power density than a 4-stroke of the same displacement. And with FVVA, common-rail fuel injection, and state-of-the-art exhaust aftertreatment, emissions should be similar to current clean diesels, or lower because the head isn't superheated by exhaust flow.
A uniflow 2-stroke diesel requires forced induction, so the LIM valves in our engine are opened by intake manifold air pressure on the “floor” of each valve. Compressed air metered into the space below the collar closes each valve at exactly the right time. LIM valves in a 4-stroke would be both opened and closed with compressed air.
LIM valves could be incorporated into conventional automotive engines, or marketed with retrofit cylinder-head kits to increase the fuel efficiency of large diesel engines in trucks, ships, locomotives, off-road vehicles, and stationary generators. This could be a disruptive innovation for valve makers, but a sustaining innovation for IC engine producers.
A numerical simulation done by Doug Baker, PhD., of TECAT Engineering, indicated a supercharged, intercooled LIM engine could reach a BSFC of 0.35lb/hp/hr and a power density of from 1.3 – 1.5 hp/cubic inch.
Next, LIM, possibly working with Ricardo who have made a proposal to study and prototype the LIM engine, will develop electronic valve controls, to include:
- designing a compressed-air distribution system.
- deciding on solenoid or piezoelectric control valves.
- calculating air pressures and volumes needed for valve actuation.
Video
-
Awards
-
2014 Top 100 Entries
Like this entry?
-
About the Entrant
- Name:Jeffrey Klein
- Type of entry:teamTeam members:Jeffrey Klein - CEO, - LIM Technology
Konstantin Mikhailov-CTO, - LIM Technology
Steve Loizeaux - retired Honda Tech Editor - Software used for this entry:PRO-Engineer
- Patent status:patented