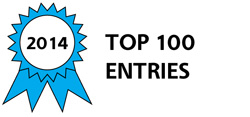
The promise of robots relieving humans of dangerous, dirty, and repetitive work in manufacturing remains largely unfulfilled, despite a half century of research and practice. This is because conventional robots work by controlling arm position--a surprisingly limiting mode of operation. They require repeatable parts, precise fixturing, consistent work, and known tool characteristics. When this is not the case, as in most operations, human labor is required.
Humans are required not necessarily for their intelligence, but to perform work better accomplished by force. For example, people can assemble closely meshing components and grind/polish surfaces without precise dimensional information; they merely apply force and let the workpiece geometry determine the motion path. Whereas position control, by design, rejects external forces, working by force allows position information to relay back to the operator. While the concept of robots working by force is not new, creating this behavior by adding force-feedback or deliberate mechanical compliance produces sluggish response and poor accuracy.
They key to human-like capability is to duplicate the dynamics of the human arm. The Touch Robot, with a patented design, achieves the requisite combination of attributes: useful levels of force, smooth, low-friction joint actuation, and agile, low-inertia links. Force dynamics are specified merely by commanding motor torques. Built with conventional servomotor technology, it consists of a 4-axis arm and 2-axis part-positioner working in concert on a workstation table. It is self-contained, portable, pre-calibrated, and operates on 120VAC and 90 psi shop. With only motor-mounted encoders for sensory feedback and a no-lube-required power transmission system, the Touch Robot is rugged enough to be deployed virtually anywhere in the plant. The intentionally limited speed, contained workspace, and modest strength that can be overpowered also make it safe to work alongside people.
An initial application was the shaping and finish grinding of gas-engine turbine blades. Turbine blades present a particular challenge because the parts require perfect smoothness on the micro level, while tolerating macro-level dimensional variations. Hand-finishing is a difficult job that presents known risks of repetitive stress injury to the operator. The Touch Robot leverages its force capability with pre-programmed, parametric material removal algorithms--similar to a human skill. The software extracts desired contours from CAD and generates appropriate toolpaths. While it works, the robot measures actual contours and compares them to the CAD reference. Excess material is identified, and new motions are autonomously generated to focus effort on the affected area. With a common datum reference between measurement and material removal, accuracy becomes a function of easily calculated differential kinematics. Thus, in a closed-loop fashion, the measured part shape is driven to match the CAD model. The finishing algorithms can be applied to a wide range of parts, produced by casting, forging, molding, and machining processes. Working by force not only makes automating tasks feasible, it makes the automation simpler, too.
Video
-
Awards
-
2014 Top 100 Entries
Like this entry?
-
About the Entrant
- Name:Steven Somes
- Type of entry:individual
- Patent status:patented