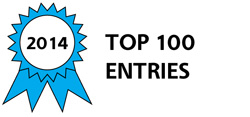
Large Hydrostatic Wind Turbine
Lower cost - High efficiency - Longer life
The energy of wind is free, but the costs of the turbines transmitting the energy into electricity are too high to be competitive with conventional ways to produce electricity.
Conventional drive systems consist of a rotor driving an electric generator through a gearbox for increasing the rotational speed to that of the generator. The systems are complex, expensive, heavy, and require high maintenance. Generators, directly driven by the rotor, operate without a gearbox but are significantly larger in size, heavier and more costly. Because of the varying generator speed, both systems require an inverter for the electric circuit.
The new hydrostatic drive system consists of a hydraulic pump in the rotor hub driving the hydraulic motor at the generator with pressurized fluid. The infinite variable displacement of the highly efficient motor is electronically controlled for driving the generator at constant speed, allowing for rotor blades shaped and adjusted for maximizing the extraction of energy form the wind without rotor speed consideration.
The motor/generator unit and all additional components are located in the container on ground level, easing the fulfillment of the requirements regarding space, weight, noise, and weather conditions, and non-turbine-specific, lower-cost components can be utilized. The hydrostatic drive for a 5 MW turbine reduces the weight on top of the tower by 50% (to125 tons) and allows for a less costly tower and installation.
The pump in the rotor is adjustable from full to a 50% flow rate, and the efficiency changes only slightly with varying speed and hydraulic pressure. The motor/generator section consists of a small and large motor/generator unit (1.7 MW, 3.7 MW), providing high efficiency over a wide power range by utilizing the small, large or both units between half and maximum pressure and 50% and full flow. The arrangement provides high overall efficiency from 0.4 MW to 5 MW. A central motor/generator unit, driven by several wind turbines, simplifies wind farm installations.
The weight of the rotor is supported by self-aligning hydrostatic bearings carrying 98% of the load hydraulically and 2% through mechanical contact forces resulting in extremely low friction, fluid losses and wear. The radial-piston forces on the driveshaft, also with a 98% and 2% load distribution, balance each other to 100% and create no bearing loads. The calculation of losses for the pump results in an overall efficiency of 96.5%, and ca. 89% for the whole drive train, from the rotor to the generator. Gears and roller bearings are not utilized and the useful life not limited.
The high efficiency, excellent controllability, low weight, and freedom of arranging the drive components independently to each other result in significantly reduced costs. The cost analysis from the US Department of Energy (NREL - LWST COE) applied to the new drive system reduces the costs of energy ($/kWh) by 21.7 %, nearly the 27% needed to be competitive with conventional power plants. (U.S. Patent)
-
Awards
-
2014 Top 100 Entries
Like this entry?
-
About the Entrant
- Name:Ingo Valentin
- Type of entry:individual
- Software used for this entry:SolidWorks
- Patent status:patented