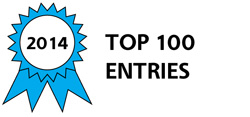
Tri-comb(tm) Panel Core Structures were created to facilitate mass production of economical, high-performance panels. The real world applications are vast. Substantial savings in weight, materials, shipping and production costs are all simultaneously possible when Tri-comb(tm) replaces conventional panels or even honeycomb. Tri-comb(tm) opens up new possibilities for better LEED compliant building materials.
We wanted a moldable high-performance panel at a bargain price. Honeycomb panels are one of the most efficient panel designs ever devised, but they are difficult and expensive to manufacture. Because of these and other design application issues, honeycomb is rarely ever used in consumer grade products. It is primarily used in expensive high-tech applications where the cost and manufacturing difficulties are justified by performance requirements and critical weight savings. Honeycomb cores require top and bottom lamination to be stable. Laminate bonding is critical for honeycomb, but it has very limited bonding surface. Delamination of honeycomb panels can cause critical failure.
The multi-patented Tri-comb(tm) core designs (U.S. Patents: 7021017, 7591114, 8609226) use a balanced matrix of reversed cells with internal bracing and a “buttress” to reinforce the structures and distribute forces. The cores are stable and strong without requiring lamination. Single or double lamination markedly improves performance. Panels can be flat or in complex curves, facilitating aerodynamic and ergonomic design applications.
Over 500 Finite Element Analysis tests were done to determine the comparative behavioral properties of Tri-comb(tm) structures vs. honeycomb for diverse requirements. The results demonstrate the high strength and efficiency of the designs. They can easily be designed to outperform honeycomb in crush, shear and bend tests while retaining substantial material efficiency improvements. Additionally, Tri-comb(tm) cores have superior bonding surface area – (see graphics).
A wide range of behaviors can be attained by optimizing cell proportions. A Tri-comb(tm) panel can do the same job with less material or do a better job with the same materials. This creates ample opportunities to intelligently lower material use and weight while still meeting exacting performance criteria.
The core structures can all be produced in simple 2-part molds in a wide range of materials. Molding was desired because it is one of the cheapest and fastest processes for making complex parts in large quantities, and the technology is very well understood. Some possible methods: injection molding, molded fiber glass or carbon composites, aluminum die-casting, metal sand-casting and 3D printing. Compressed or engineered wood panels should also be possible. Ideal methods will depend upon applications.
Some possible uses: new alternative green construction materials for bridges, buildings, furniture, cabinets, shelves, impact resistant packaging, automobiles and trucks, trains, motorcycles, aircraft, marine and spacecraft. Very high compression, shear and bend resistance make Tri-comb(tm) ideal for high-pressure applications; for instance, construction for hurricanes or deep-water.
In our future, limited by dwindling raw materials and ever increasing costs, less has to do much more. Tri-comb(tm) raises the bar for high-performance products, while making high-performance a truly efficient choice for low-cost mass production consumer products.
Please visit http://www.tri-comb.com/ for more information.
-
Awards
-
2014 Top 100 Entries
Like this entry?
-
About the Entrant
- Name:Warren L. Herron
- Type of entry:individual
- Software used for this entry:Strand7
- Patent status:patented