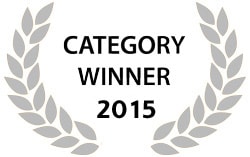
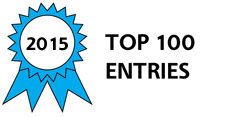
Our team at NASA's Armstrong Flight Research Center has developed fiber optic sensing system (FOSS) technology that represents a major breakthrough in high-speed operational monitoring and sensing. Driven by ultra-efficient algorithms, FOSS can be used to determine in real time a variety of critical parameters, including strain, shape deformation, temperature, liquid level, and operational loads. This state-of-the-art sensor system delivers reliable measurements in the most demanding environments confronted by aerospace, automotive, and energy sectors. FOSS is ideal for monitoring the structural health of aircraft, buildings, and dams; improving the efficiency of turbines and industrial equipment; detecting instabilities within tunnels and power plants, and much more.
The system offers unprecedented levels of spatial density, as each of the eight 40-foot hair-like optical fibers provides up to 2,000 data points with adjustable spatial resolution for a total of 16,000 sensors per system. To achieve these revolutionary capabilities, FOSS employs fiber Bragg grating (FBG) sensors and a combination of optical frequency domain reflectometry (OFDR) for high spatial resolution and wavelength division multiplexing (WDM) for high acquisition speed, together with an interferometer technique that can simultaneously interrogate thousands of FBG sensors on a single fiber. Each of the 16,000 OFDR sensors can be sampled up to 100 samples per second while several dozen of these sensors can be sampled at rates up to 35,000 times per second for high dynamic applications.
The real-time algorithms and processing system measure strain at multiple locations along the length of the fiber while attached to the surface of a structure. Strain data can be correlated into displacement data, thereby displaying the shape and movement of the fiber (and therefore the shape and movement of the attached structure). The end result is that strain can be displayed in real time as the optical fiber is moved. From these strain measurements, the system calculates 2D and 3D shape, stress, temperature, pressure, stiffness, liquid level, and operational load.
Traditional sensing systems are based upon the use of copper wire, significant amounts of coating materials, and metal sensing parts. To achieve the same number of sensing points as the FOSS system, conventional systems would comprise hundreds of pounds of metals and plastics. In contrast, FOSS acquires a large number of key engineering measurements in real time for large structures that are undergoing a wide range of displacements during operation. With thousands of sensors on a single fiber, sensors can be placed at 1/16-inch intervals (e.g. within bolted joints and embedded within composite structures), enabling precise, high-resolution measurements in locations where conventional strain gauges will not fit. FOSS accomplishes all this with a few ounces of flexible industry.
Video
-
Awards
-
2015 Electronics Category Winner
-
2015 Top 100 Entries
Voting
-
ABOUT THE ENTRANT
- Name:Lance Richards
- Type of entry:teamTeam members:Patrick Chan, Optics Engineer
Philip Hamory, Electrical Engineer
Allen Parker, Electrical Engineer
Anthony Piazza, Instrumentation Specialist
Lance Richards, Structures Engineer
Dr. William Ko, Structures Engineer - Lance is inspired by:The inspiration for our team is a desire to answer the question, “What if?” What if we can do X faster, smaller, less expensive, all around better? We constantly ask ourselves this question and are not satisfied until we find solutions.
- Patent status:patented