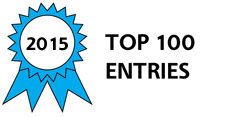
The piezoelectric rotary actuator is a new positioning device, providing exeptional dynamics and accuracy even if connected to heavy loads. The main applications are tracking, guidance, deflection and positioning systems (e.g. antenna, laser, telescope, camera, mirror), aileron control, locking systems and valve actuation.
Since the commercialization of piezoelectric injection systems within the automotive industry, piezostacks have become a commodity. These robust actuators offer high actuation forces, typically of several thousands of newton and superior dynamics, with switching times in the range of microseconds at operating frequencies up to several kilohertz. Piezostacks are available at different form factors at fairly low costs. Unfortunately, due to the magnitude of the inverse piezoelectric effect, until today their application is limited to short stroke actuation in the range of 50 um to 100 um.
The piezoelectrical torsional actuator is a new straight forward approach to solve this problem by converting the tiny stroke of piezostacks by means of a frame structure into amplified rotational movement without impacting the dynamics and the forces. The piezoelectric rotary actuator consists only of four parts: two endplates, the frame structure and the piezostack itself. It can easily be manufactured from common materials and technologies at low costs. Electric charge applied to the piezostack by a voltage or current source, is converted without any delay into amplified rotational movement. As the rotational movement is directly proportional to the electric charge of the piezostack, the piezoelectric rotary actuator can be operated feed-forward controlled as well as closed-loop controlled.
Compared to commercial deflection or tracking systems, like galvos or solenoids, the piezoelectric rotary actuator exhibits much higher stiffness and actuation forces combined with instant reaction at typical response times of microseconds and thereby is able to carry much higher loads at increased dynamics and accuracy.
The motion converter (frame structure), consists of a plurality of rod like shaped arms surrounding the piezostack. The arms are slightly tilted against the longitudinal axis of the piezostack and connected to endplates which case the piezostack at the end faces. Additionally the frame structure serves as a mechanical preload spring for the piezostack. A preferred design of the frame has a symmetrical structur, with a ring shaped connector (equator ring) for the load (e.g. mirror) at the medium of the piezostack, to which two groups of arms with opposite orientation are connected. As the arms tend to align with the longitudinal axis if the endplates are displaced by the piezostack, the equator ring is put into amplified proportional rotational movement. Power consumption is proportional to the operating frequency and zero if a position is kept. During slow motion guidance, e.g. space tracking applications, which might be interrupted by intermittent fast movements, a small battery is sufficient for long time operation. By combining two or more piezoelectric rotary actuators, the operation can be extended to synchronised multi axis deflection. Robustness and reliability are high, as any wearing parts are avoided.
Video
-
Awards
-
2015 Top 100 Entries
Like this entry?
-
About the Entrant
- Name:Andreas Kappel
- Type of entry:individual
- Software used for this entry:AutoCad Inventor Professional
- Patent status:pending