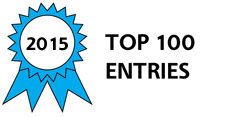
Although counter-intuitive, evolutionary internal combustion engine concepts are often times preferred over revolutionary ones. Although intriguing theoretical engine designs abound, a truly revolutionary engine concept’s value is questionable if it can’t be produced in quantity, inexpensively, and also provide reliable service. On the other hand, traditional reciprocating internal combustion engines are well understood, and the tooling used to manufacture them is inexpensive and widely available. For this reason it makes sense to improve on existing engine technology, and to provide incremental improvements rather than replace them with radically new designs that may have tricky engineering or manufacturing challenges of their own.
AET’s patent pending transfer port technology is meant to improve existing reciprocating internal combustion engines’ pumping efficiency, exhaust scavenging ability, and resistance to pre-ignition, all of which ultimately improve engine efficiency, while using commonly available automotive components and simple tooling.
We have measured an increase in pumping efficiency by as much as 35% using our in-house engine dynamometer, and this improvement was accomplished by eliminating the need for separate poppet valves for the intake and exhaust cycles. Poppet valves are by far the largest restriction in an engine’s intake and exhaust tracts, and this problem is exacerbated in small engines where the available valve area is compromised by the size of the combustion chamber. The transfer port alleviates this problem by utilizing only one valve per cylinder, which allows for a much larger valve, and consequently a much better flow path.
Engines sold today are also typically knock-limited, and as a result power and efficiency are compromised by running conservative fuel and ignition timing. This is both wasteful and damaging to the environment. Pre-ignition (and subsequently knock) often begins when the end-gas in the combustion chamber comes in contact with a hot-spot, like the edge of a hot exhaust valve. But since the intake air charge flows over the same valve as the exhaust in our engine, the valve surface operating temperature is reduced along with the chance of knock. This would allow an engine to be tuned to make more power, or make the same power with a lower fuel octane requirement.
The transfer port technology also offers enhanced exhaust scavenging ability and exhaust gas recirculation. This is because the poppet valve and the flow path into and out from the cylinder are independent. The secondary valve plate can either block off exhaust flow when the poppet valve is open to enhance EGR and fuel efficiency, or it can open both the intake and exhaust paths to create a cross flow over the poppet valve during the exhaust phase to improve power.
The wonderful thing about this valve train layout is that it doesn’t rely on questionable theoretical concepts, it doesn’t require any exotic and/or expensive technologies, and the parts it does use have offered reliable service for decades. Our technology is a substantial improvement on a technology that’s been around for well over 100 years, and we are currently finishing optimization of our prototype on our dynamometer.
Video
-
Awards
-
2015 Top 100 Entries
Like this entry?
-
About the Entrant
- Name:Rick Pelfrey
- Type of entry:teamTeam members:Dale Pelfrey, Rick Pelfrey, Jim Kopasko, Geoff Hollis, Jordan Gartenhaus
- Software used for this entry:Solidworks and Ansys
- Patent status:pending