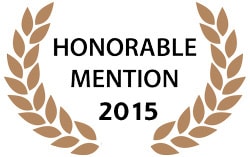
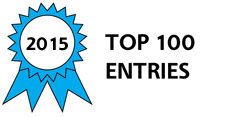
PROBLEM
Two common problems with turbocharging systems are noise and turbo lag. Closure, or partial closure, of the engine throttle while the turbo compressor is operating at high boost condition can causes excessive back pressure on the compressor creating a condition called surge. This pressure spike is damaging to the turbo bearings and compressor wheel and creates significant noise. A compressor recirculation valve (CRV. A pressure relief valve, also known as a compressor by-pass valve, diverter valve, and blow-off valve) can address this issue. However; when the valve opens, all, or nearly all, of the boost pressure is lost, thus exacerbating another problem, turbo lag. Turbo lag is the time delay between the operator’s demand for more power and when the engine delivers the demanded power. This delay is particularly troublesome during rapid deceleration-acceleration maneuvers.
SOLUTION
A team of engineers at Dayco has been working on solutions to the above mentioned problems. This team has developed unique intellectual property, including patent 9,068,535, a variable flow compressor recirculation valve. Submitted for consideration in the COMSOL “Create the Future” Design Contest 2015 is this valve concept.
Dayco’s unique valve design features make precise control of the boost pressure possible. Referring to Figures 1 (100 numbers) and 2 (200 numbers), features include a shaped valve surface (180) and position feedback through the position sensor (120) which picks up valve position through the magnetic field create by the magnet (150) housed in the valve. Control of the valve position allows better control of the boost pressure, which in-turn allows the minimum amount of pressure relief required to prevent surge. When the drive again demands power, boost pressure in the system is higher and thus builds to the required level more quickly, reducing turbo lag.
SYSTEM OPERATION
• Compressor (240) is boosting air pressure in the intake pipe (210).
• Throttle (200) closes.
• Pressure in the intake pipe rapidly increases creating the potential for excessive back pressure on compressor creating the potential for surge noise.
• PCM (230) commands poppet (170) open to a certain degree based on the pressure relief required.
• Poppet opens through vacuum applied at vacuum port (110).
• Shaped poppet surface (180) allows opening of an increasingly large annular ring to relieve intake pipe pressure.
• Position sensor (120) sends signal to PCM indicating position. PCM adjusts as necessary.
See figures for illustration of the above.
Injection molded plastic, as molded, can be used to make all of the primary CRV components.
Precise control of the boost pressure through the use of Dayco’s unique compressor recirculation valve can allow the prevention of surge through the turbochargers operating range and reduce turbo lag.
-
Awards
-
2015 Automotive/Transportation Honorable Mention
-
2015 Top 100 Entries
Like this entry?
-
About the Entrant
- Name:James Miller
- Type of entry:teamTeam members:Dave Fletcher, Matt Gilmer, Brian Graichen, Keith Hampton, James Miller, Andy Niedert
- Software used for this entry:Solidworks
- Patent status:patented