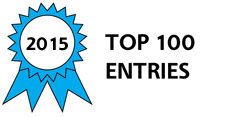
This valve design has a novel hollow, balanced piston, which is moved into an open or closed position against a stationary solid seat within the valve body by using the working fluid or an external pressure source to seal the valve.
The novel balanced piston can be designed to always seat with the same amount of force allowing the use of metal-to-metal seats as well as soft seats. It is designed so that, even when used in high-pressure applications, it does not require a large conventional valve actuator, and the valve stem itself is eliminated. Actuation is achieved with the use of small, simple solenoid or hand valves. This design also eliminates the need for many seals used with existing ball valve and globe valve designs, which commonly cause failure. Coupled with the elimination of the valve stem and conventional valve actuator, this valve design reduces downtime and maintenance costs, while increasing valve reliability and seat life.
This technology is applicable for all pressures (15-15,000+ psi), with a floating piston design, used for controlling a flow of a pressurized working fluid. The prototype valve is an open/closed, non-positionable piston capable of using metal to metal seats without requiring seat sliding action. The valve is designed to use mechanical actuators and be positionable, if desired. This design eliminates issues associated with large high pressure ball valves and globe valves, as well as stem wear, stem leakage, and seat wear; the need for conventional large and/or motor driven/actuators is also eliminated. A hollow, moveable piston is pressed against a solid stationary seat by allowing the working fluid pressure or an external pressure source to act on a specific working area of the piston while venting an equal area, thus pushing the piston against the seat. Reversing the pressurized area and vented area allows the piston to move off of the seat and thus open the valve. The working fluid then flows around the stationary seat and is channeled through multiple passages back into the flow pipe path. To reseat the valve, the pressurization and venting are reversed again moving the piston back onto the seat. This allows the moveable seat to be pressed against the stationary seat again, and it is reseated. Because the balanced piston does not require large forces to move, and the pressure change across the valve does not impose force on the piston, significantly less energy is required to operate the valve. This may allow remotely located valves to be operated for many cycles using internal pressure or a small accumulator instead of having to run tubing from an external source. Wireless technology can then be applied to make the valves true plug and play hardware.
Sized for 10 inches; manufactured from a variety of metals; only five major parts without stem seals or packing glands that can leak; no external actuator; stationary metal to metal seat improves reliability; use in pressurized tanks, severe duty, extremely high pressures, temperatures, very fast actuation applications.
-
Awards
-
2015 Top 100 Entries
Like this entry?
-
About the Entrant
- Name:Gigi Savona
- Type of entry:individual
- Software used for this entry:NA
- Patent status:patented