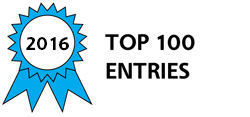
The Clarke-Brayton Engine has the potential for 55% brake thermal efficiency compared to 42% for state-of-the-art conventional diesels, is dramatically more compact than conventional engines of the same power, can burn diesel or natural gas as compression-ignition fuels and is less expensive to manufacture. Two prototypes have been manufactured and tested, the latest of which has demonstrated 45% indicated thermal efficiency, including losses for gas mixing and pumping. The test results have shown a clear path to 59% indicated thermal efficiency.
As shown in the submitted video, the engine is composed of modules of three cylinders – an intake cylinder, a smaller bore combustion cylinder, and an expansion cylinder with the largest bore. Air moves sequentially from intake to combustion to exhaust via valved transfer passages.
Market Attractiveness
Such an engine is a low cost way of dramatically improving fuel efficiency in many markets including power generation, trucking, automotive, and marine. The fuel efficiency itself reduces greenhouse gas emissions, but utilizing natural gas further reduces GHG emissions while enabling increased reliance on domestic energy production. Implementing this solution requires no updates to infrastructure or drastic changes to vehicles or application structures.
Manufacturability
The engine utilizes conventional manufacturing methods and tooling currently being used in the production of engines and does not rely on any unproven, expensive or time-consuming methods. Materials, likewise, are conventional.
Reasons for high efficiency
There are three primary reasons for the high efficiency:
1) Use of the Brayton Cycle – expansion to ambient pressure allows more work per cycle.
2) Compression ratio in excess of 50:1 – Reactants at higher internal energy states reduces exergy destruction during combustion.
3) Low surface area for heat loss – combustion cylinder bore is much smaller than the intake bore for a compact combustion chamber leading to less heat loss and a more efficient engine.
Taking advantage of these benefits requires that losses during transfer between the cylinders are significantly smaller than the improvements offered by the design. Careful coordination of piston phasing, valve timing and size, and transfer passage geometry is critical to minimizing transfer losses.
Reasons for compactness
1) Short stroke relative to the intake cylinder bore leads to smaller engine size.
2) Power stroke every revolution – while this is not a two-stroke engine, it does have a combustion cycle every revolution, enhancing power density over a conventional engine.
Reasons for low manufacturing cost
1) Less material due to small engine size.
2) No turbos.
3) No intercoolers.
4) 1/3 as many fuel injectors.
Reasons for being able to use Natural Gas as CI fuel – The high compression ratio reduces the ignition delay of methane from hundreds of degrees of crank angle to less than one degree.
Video
-
Awards
-
2016 Top 100 Entries
Like this entry?
-
About the Entrant
- Name:Edward Omalley
- Type of entry:teamTeam members:Edward O'Malley John Clarke
- Software used for this entry:Solidworks, Solidworks Simulation, Engineering Equation Solver (for thermodynamic simulations)
- Patent status:patented