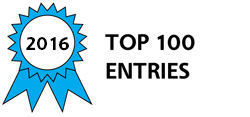
Two factors are leading automakers to reduce the weight of their automobiles. In 2025 the US CAFE standards for fuel economy for light vehicles such as passenger cars is 54.5 mpg. In addition Green House Gas (GHG) and CO2 emission regulations are forcing automakers to look at electric powertrains which are heavier than internal combustion engines. “Lightweighting” is one method auto makers are investigating to meet the fuel economy, GHG and CO2 requirements in their vehicles. Lightweighting is the substitution of stronger, lighter weight materials for standard automotive sheet steels. Ford recently introduced a Ford F-150 pickup truck that uses aluminum alloys in a large number of parts to reduce vehicle weight and improve fuel economy.
Aluminum alloys have two disadvantages for automakers. First, the aluminum alloys have a much larger carbon footprint than steel alloys. (The carbon footprint of materials is important for European consumers.) In addition, parts suppliers to the automakers have a material handling infrastructure that has been designed for steel not aluminum. For example, electromagnets are used to move sheet steel blanks into the stamping presses in the production of cold stamped steel body parts. Aluminum sheet alloys will require all new material handling equipment for the cold stampers of auto parts.
Steel companies have started to develop new Advanced High Strength Steels (AHSS) to compete with aluminum alloys as lightweighting materials. To aid the development efforts, the US DOE has set strength and ductility targets for the new 3rd Generation of the AHSS alloys (3rd GEN AHSS).
CarTech Temper Tough®-HD and –LN Alloys are high strength, high ductility quenched and tempered sheet and strip steels which exhibit superior combinations of UTS and EL over other AHSS alloys and the DOE Targets for 3rd GEN AHSS as shown in the attached graph and table. Temper Tough-LN contains lower alloy content and therefore costs less than Temper Tough-HD alloy. US and foreign patents are pending for both alloys which have been produced as strip from 40 ton (36.3 metric tons) continuous cast heats.
The DOE targets shown in the graph and table were set for fully heat treated sheet and strip to allow for cold forming (cold stamping). Parts can also be hot stamped. But hot stamping requires more processing equipment (re-heat furnaces in particular) than cold stamping and is more available in Europe than in the US.
By providing properties in excess of the DOE Targets and other AHSS alloys in a fully heat treated sheet and strip, Temper Tough-HD and –LN alloys allow automakers to utilize steel to attain lightweighting goals in their car designs. In addition, the automotive cold stampers can now supply 3rd GEN AHSS parts to the automakers without costly investments in equipment for hot stamping.
-
Awards
-
2016 Top 100 Entries
Like this entry?
-
About the Entrant
- Name:Paul Novotny
- Type of entry:teamTeam members:Paul M. Novotny Patrick C. Ray Michael E. Wilkes Vincent T. Russell Dudley J. Merchant Shane A. Para David L. Strobel
- Patent status:pending