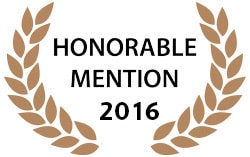
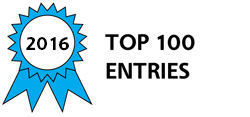
Autokinetics AK12EV Ultralight Electric Bus
The concept for this advanced bus design originated with two small grants from the US Department of Energy, and culminated in the fabrication of a proof of concept prototype. A next generation, production ready design is currently under way.
The AK12EV features a low floor architecture from front to rear, for improved handicap and passenger access, with independent suspension on all four corners for better ride and handling qualities. It is an entirely new and unconventional design with major departures from traditional buses in the areas of body structure, suspension, brakes, propulsion, doors, and seats. The result is a full size city bus that achieves the equivalent of 32 mpg, whereas a standard diesel bus gets only 3.5 mpg. The range of the zero-emissions battery electric version is 150 miles. A plug-in hybrid version will be available with a small engine/generator unit which will extend the range to 300 miles. Capacity is 45 seated occupants and 50 standees.
The unibody structure of the bus consists of a monocoque shell similar to the fuselage of an aircraft except that it is made entirely of high strength stainless steel (AK Steel Nitronic 30, cold rolled to 120 ksi). There is no separate frame, so the underside is completely smooth for better aerodynamics. The floor and roof are constructed of spot welded, corrugated core stainless steel panels. The roll-formed side wall pillars are designed to withstand a side impact from a SUV travelling at 25 mph. Through the use of high performance materials and innovative design a weight savings of over 50% has been achieved, while improving both strength and stiffness.
Manufacturability was a prime consideration from the beginning of concept development. A detailed cost study indicates that in spite of the higher cost of stainless per pound, the finished body structure will be over 30% cheaper to build. Additionally, the capital investment will be a small fraction of that required for conventional buses. Since stainless steel does not need to be painted or otherwise protected from corrosion, the huge investment for a paint shop and bake ovens can be saved. It is expected that these buses will be built in geographically distributed micro-factories. This saves the cost of shipping and creates manufacturing jobs in cities all across the nation.
The reduced weight allows the downsizing of motors, batteries, wheels, tires and other components. These represent important cost savings, especially in an electric vehicle of this size. The smaller tires also mean that the wheelhouses can be lowered and used to increase the seating capacity.
The suspension is a sophisticated SLA (short/long arm) type with all stainless steel components. The spring/damper units are an air-over-oil design that allows for ride height control and kneeling. The prototype uses one hub mounted electric motor at each rear wheel. A single speed planetary reduction gear is integrated into the hub design. Future versions of the full size bus will have 8 wheels and 8 wheel drive, using direct drive in-wheel motors.
Video
-
Awards
-
2016 Automotive/Transportation Honorable Mention
-
2016 Top 100 Entries
Like this entry?
-
About the Entrant
- Name:Bruce Emmons
- Type of entry:teamTeam members:Autokinetics Inc US Department of Energy AK Steel
- Software used for this entry:Pro-Engineer and SolidWorks
- Patent status:none