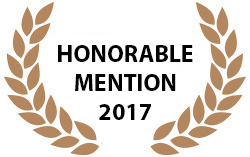
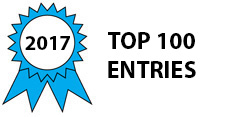
Cast iron automobile brake rotors are heavy and suffer from limited lifetimes and excessive wear in the form of dust. Aluminum (Al) metal matrix composites (MMCs) with ceramic particulate reinforcement such as silicon carbide (SiC) have long been considered as significantly lighter weight, potentially longer lasting and more environmentally favorable automobile brake discs; however, previous efforts to introduce MMC brake rotors into automobiles have had limited success only in smaller, lighter mass vehicles. Thermal management of the discs has been problematic, because the ceramic has much lower thermal conductivity than the metal matrix. Other limitations are due to processing techniques which result in defects such as porosity, agglomeration of ceramic particulates, and formation of undesirable phases such as aluminum carbide.
ATS-MER has solved these problems with a novel patent-pending, lower temperature, hot pressing technique, which allows for uniaxial hot pressing with the MMC matrix in the molten state. The difficulty in keeping low viscosity molten metals sealed in a die at elevated temperatures while applying pressure has precluded the technology from being utilized previously. This unique processing technology which substantially eliminates porosity and defects has been combined with a cost effective, performance enhancing hybrid sandwich type configuration to take advantage of a high thermal conductivity Al alloy core, with thin, wear resistant MMC surface layers. ATS-MER has been developing such brake rotors with three objectives in mind: (1) improve upper temperature capabilities, (2) eliminate wear and dust generation, and (3) demonstrate economic feasibility. The first two objectives have been fully realized, and a continuous rather than batch process is being designed and implemented to achieve cost objectives. A slightly higher cost point compared to cast iron rotors is justified considering the MMC rotors will last the lifetime of the vehicle as well as substantially eliminate dust generation. ATS-MER’s MMC brakes are in qualification for 2018 models with full implementation expected by 2019.
Currently, Al-SiC MMC hybrid brake rotors have been fabricated with outer diameters greater than 400 mm and thicknesses up to 42 mm, and these have successfully passed full-scale dynamometer and vehicle testing with exceptional results, resulting in almost 10 times the number of maximum cycles possible using cast iron discs (before the brake pads, and not the MMC rotor, failed), while incurring much lower maximum operating temperatures of 340-400°C compared to 650-700°C for cast iron. There was essentially no wear and ≤99.6% less particulate generation of the Al-SiC MMC discs compared to that observed for the same testing with cast iron rotors. Other attributes of MMC rotors compared to cast iron brake rotors include being up to 50-60% lighter leading to a reduction of unsprung weight and improved ride and handling. Due to the lighter weight and reduced inertial forces, lower CO2 emissions are also incurred. Thus, ATS-MER’s novel Al-SiC MMC brake rotors offer significant environmental benefits of much reduced dust generation and lower CO2 emissions, a more comfortable ride, and elimination of the need to replace the rotors over the life of the vehicle.
-
Awards
-
2017 Automotive/Transportation Honorable Mention
-
2017 Top 100 Entries
Like this entry?
-
About the Entrant
- Name:Lori Bracamonte
- Type of entry:teamTeam members:Lori Bracamonte James Withers
- Patent status:pending