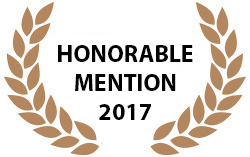
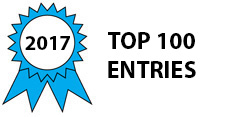
Synchronous/Switched Reluctance Motor/Generators (SRM) have great potential for many applications which require rugged construction and high reliability at low cost such as wind turbine generators or tractive drive motors. Widespread use of SRM's is limited because of magnetic circuit reluctance patterns that contribute to cogging torque. Our unique geometry eliminates cogging torque without complex software using prime numbered stator armature coils. The advantages include:
1) Simple low cost all steel rotor design using primed numbered step sequence commutation for smooth rotation.
2) Easy to assembly design comprising only 4 sub-assemblies
- Rotor has no copper for increased thermal and electrical efficiency
- Stator
- Electronic commutator located adjacent to stator winding inside machine's frame. Each H-bridge solid state switch functions in the same manner as a mechanical commutator conveying current to each individual coil in step sequence
- Frame provides structural support for the stator and rotor.
3) Thermally 'cold' rotor lacks windings or squirrel cage for added reliability and extended bearing life. This feature also obviates the need for ventilated frame cooling as the rotor does not need to be cooled internally in comparison to an induction or d.c. brushed machine with a rotating armature.
4) Can be retrofitted inside existing D.C. brushed (and/or A.C. induction/synchronous) frames and re-purposed as a 'drop-in' replacement upgrade from brushed machine topology to brushless reducing maintenance cost dramatically.
Design:
Our stator design begins with the stator core comprising slots equal to twice the prime number of stator coil windings. This arrangements producs a single (radial) direct axis with each coil having a slightly different reluctance for smooth rotation without mechanical pulsations.
The rotor is comprised of a steel shaft and silicon steel laminations resulting in a lower moment of inertia and is designed to be magnetically coupled with the stator without copper windings or bars. As the stator coils are energized, the rotor follows the rotating wave in sync or without slippage.
The electronic commutator comprises a plurarity of MOSFET/IGBT solid state switches arranged in an annular layout located in close proximity to the stator coils in similar manner to a mechanical commutator. However, unlike a mechanical commutator, our electronic commutator can turn itself on and off obviating the need for a separate external controller. The H-bridge switches are turned on and off in sequence generating a strong rotating magnetic wave and PWM circuitry limits inrush current for smooth starts with low thermal/mechanical stress.
Applications include:
1) tractive drives for rail and automotive vehicles.
2) low speed direct drive wind turbine generators
3) high speed centrifugal compressors
4) low cost brushless motors for hand held power tools and appliances
5) industrial motors with integrated drives
6) explosion proof drives
-
Awards
-
2017 Machinery/Automation/Robotics Honorable Mention
-
2017 Top 100 Entries
Like this entry?
-
About the Entrant
- Name:Douglas Richard
- Type of entry:individual
- Software used for this entry:SolidWorks
- Patent status:pending