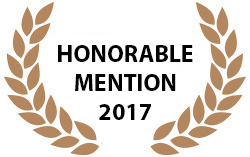
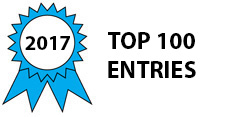
One of the most commonly employed technologies of additive manufacturing is fused deposition modeling (FDM). FDM that employs polymer as the based material has proven to be a powerful method in rapid prototyping. Most of the FDM 3D printer feed stock material is Polylactic Acid (PLA), Acrylonitrile-Butadiene-Styrene (ABS), Nylon and etc. These limited choices of material for FDM printing had limited the option for engineers to create an object with a blend of different materials to create something unique where the object is being optimized not only in terms of shape but also the used of different materials to create an efficient product. Currently, the available 3D desktop printers on the market have a small build volume, mostly only enabling one or multiple materials to print at once, the blend of different material is discrete which imposes weak linkage material structure. However, this can be changed if a new mechanism of unique extruder exists in the printer where it can print out product which doesn’t limit by the stock feed filament sell on the market. The bending of material can be customized by the user. Unique property of material can be printed out off-the-shell without the need of third party development on the filament required. To realize this ultimate ideal, it had imposed a high challenge on the capability of the machine, where it must be able to print and blend multiple materials at once while obtaining a high-resolution printing.
The solution is presented in our newly design unique FDM printer. The printer has a compact mixer which is able to take in two different materials with control algorithm to produce the desired mixing ratio. The different mixing ratio of the polymer can produce unique mechanical properties of material, for example with the nylon as based matrix polymer and carbon fiber as filler, different mixing ratio between these materials can produce varied stiffness in the material. This mixture will be extruded to print out the object intended by the user. This opens a new design paradigm to product design and development, for example product which requires texture of the soft handle and rigidity in the core can be easily realized in a single print without the need of different material glue up together. The blending of the texture and the core structure is in smooth transition with rigid material bonding. This opens the new opportunity to the material researcher to explore different blending of materials to create customize material properties for unique product design. Conventional methods can’t offer such flexibility. The process is controlled with the use of a PC-based PLC system incorporated with smart AI control algorithm which makes it possible to upscale the printer design to handle large object printing.
Video
-
Awards
-
2017 Machinery/Automation/Robotics Honorable Mention
-
2017 Top 100 Entries
Like this entry?
-
About the Entrant
- Name:Jing Yuen Tey
- Type of entry:teamTeam members:Dr Tey Jing Yuen Dr Yogeswaran a/l Mohan
- Patent status:none