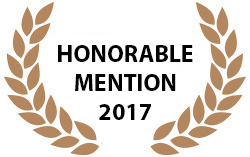
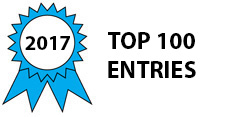
Gear systems are one of the oldest and most iconic forms of engineering. They have been studied for so long and by such great minds (Archimedes, da Vinci, etc.) that breakthroughs are rare. Mainstream technologies include the Cycloid (circa 1970), Strain Wave (circa 1950), and Planetary (circa 100 BC) drives. The Orbitless (pat pend) drive is the first new low-ratio drive since the Planetary which shares many features such as torque splitting and co-axial drive shafts that spin in a common direction. However, it has advantages such as lower production cost and lower internal speeds leading to much higher efficiency and longer bearing life.
Orbitless and Planetary drives are mechanically very similar. Both have a sun gear (the input), planet gears, and a carrier (the output) that supports the planets on a set of bearings. However, a Planetary drive also has a ring gear whereas an Orbitless drive has a second carrier that is connected to the planets by a second set of bearings. The result is a drive with half as much tooth engagement and which provides half the reduction ratio. This services a need for ratios that are not possible with a Planetary drive which has a practical lower limit of around 3:1 whereas an Orbitless drive can provide ratios as low as 1.5:1.
All of the parts in an Orbitless drive also exist in a Planetary drive. However, the most costly and difficult to produce part, the ring gear, is avoided. Ring gears are large, narrow, and have internal teeth. The internal teeth require special tools and processes to cut. The large size requires large machinery or must be produced in multiple sections. And the narrow body deforms when it is heat treated or manufactured from soft materials such as plastics. Consequently, ring gears are often the most expensive and inaccurate component in a Planetary drive and account for most of the energy losses.
Orbitless drives have been adopted by two world leaders in high precision actuators, Micromo-Faulhaber and Maxon Motor. Each has developed a prototype Orbitless drive to service a different market segment. A test comparing a Micromo Orbitless and Planetary drive showed gear-head energy loss reductions from 43% to 59%. In comparison, prior efforts to improve efficiency by tooth geometry or other parametric changes rarely exceeded 1%. The current prototypes are miniature (<30mm) and intended for the robotics, medical, automotive and aerospace markets, but the technology can be scaled up to accommodate heavy machinery or energy generation plants without sacrificing its technical benefits.
In automation, friction impedes controller stability, speed and accuracy. The unmatched efficiency of an Orbitless drive comes from ultra-low friction which translates into higher throughput and lower production costs for automated factories, electric vehicles with longer battery range, more compact ambulatory medical devices such as infusion pumps for diabetics and cancer patients, and countless other advantages to an infinitely diverse range of motorized products. An Orbitless drive is currently being developed by two industrial partners to satisfy these needs.
Video
-
Awards
-
2017 Machinery/Automation/Robotics Honorable Mention
-
2017 Top 100 Entries
Like this entry?
-
About the Entrant
- Name:Leo Stocco
- Type of entry:individual
- Software used for this entry:Solidworks
- Patent status:pending