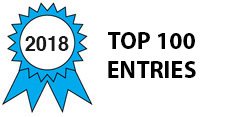
GREAT PLAINS DIESEL TECHNOLOGIES, L.C. (GPDT)
GPDT offers continuous direct control of diesel fuel injector needle lift, to control fuel injection flow rate. This is but one application of a robust, durable mechatronic actuator technology.
Origins
In the early 2000s, increasing the speed at which a fuel injector could open and close helped reduce emissions. A faster solenoid was needed to more rapidly shuttle the injector servovalve which in turn directed fuel pressure to only open or close the injector needle. First applied to injectors in 1913, physics limits solenoid speed.
United States Patent 7,255,290 embodies a theory for how to speed up the servovalve using a different actuator technology. After 7,255,290 issued, GPDT was incorporated to test the speed theory.
Key Features
Indestructible quantum effect packaged into GPDT's actuator.
GPDT's latest injector design has no servovalve.
Needle lift is proportional to electrical current flowing through the actuator. Because current can be held steady for any length of time anywhere in its range, the needle can be stopped for any length of time at any intermediate lift anywhere in its range, thus varying at will the rate at which fuel is injected.
Needle speed is proportional to the rate at which current increases or decreases.
Tests prove these control features.
Speed Demonstrator Test
The original speed demonstrator was an actuator only, a test of the speed theory. It used fuel pressure to highly preload the actuator per the theory. Speed and lift significantly exceeded prediction. For a full test report, refer to SAE paper 2011-01-0381.
When compared with typical injector needle lifts of a few hundred micrometers, GPDT's test data, Fig 1, show that the servovalve is unnecessary. Its time delays, inflexibility, fragility, sensitivity, size, cost, and complexity then also disappear.
Preliminary Engine Test
GPDT's first engine test adapted an available GPDT actuator to an existing diesel fuel injector. (Fig 2) The OEM injector solenoid and servovalve were replaced by the GPDT actuator and custom hydraulic compensation chamber. The actuator, operating through the hydraulic chamber, directly lifted the injector needle.
A stock solenoid injector was tested for comparison. The GPDT injection profile was a pilot followed by a main charge. The difference between one set of runs is that the pilot lift was varied by one micrometer. This cause was followed by effect: the delay after the pilot after which the main charge ignited varied linearly with pilot lift, a clear demonstration of the fine control GPDT's actuator possesses. (Fig. 3)
How GPDT's Technology Enables Cost-Effective Implementation of Carnot and Diesel
Continuously vary fuel injection rate by lifting needle to any position at any speed, without bouncing.
To prevent impact fatigue, continuous electrical control reseats needle with near-zero contact velocity.
With engine running, injector can adapt to best use diesel, biodiesel, gasoline, jet fuel, ethanol, etc.
Inject closely-spaced minute quantities or "fuel dots" as needed.
Make engine run "lean, mean, green," and/or quiet at any time by appropriate electrical input.
-
Awards
-
2018 Top 100 Entries
Like this entry?
-
About the Entrant
- Name:Charlie Bright
- Type of entry:individual
- Software used for this entry:Matlab
- Patent status:patented