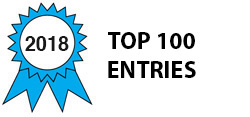
In a total hip arthroplasty (THA), arthritic bone ends and damaged cartilage are removed and replaced with a hip implant. Over 800,000 total hip replacements are performed worldwide annually. Total hip arthroplasty is one of the most clinically successful surgeries and improves quality of life for debilitating hip disease patients. Nevertheless, 10-20% of the operations undergo a revision surgery, where risk is especially high for elderly patients. One of the common reasons of a revision surgery is loosening of the stem, which can be caused by bone resorption. Bone resorption also increases the bone fracture risk and makes revision surgery more complex.
Naturally, the femur carries load from the femoral head through the femoral neck to the cortical bone of the proximal femur. Most hip prostheses are made of solid metal and are stiffer than femur bone, so the implant takes a portion of load away from bone and reduces the stress in it. This is called stress shielding. Per Wolff’s Law, bone remodels itself to adapt to external loading. Bone resorption and degeneration can occur since the load through it is reduced.
Topology and lattice optimization were performed using OptiStruct to generate the concepts and design a solid lattice hip prosthesis where stress shielding and prosthesis fatigue were considered. By optimizing the stiffness and strength of each section and each lattice ligament, the optimized design reduced stress shielding by more than 50% when compared to a conventional generic implant, and the fatigue life met the ISO standards. Additionally, manufacturability with 3D printing was considered in the design process and a Ti-6Al-4V prototype was printed with an EOS selective laser melting machine.
In the short term, this methodology can be applied to design standard prostheses. In the long term, customized prostheses can be designed and printed with each patient’s femur geometry and bone material properties that are captured by Quantitative Computed Tomography, achieving the optimum treatment outcomes for each individual.
-
Awards
-
2018 Top 100 Entries
Like this entry?
-
About the Entrant
- Name:Yuhao He
- Type of entry:teamTeam members:Yuhao He
Drew Burkhalter
David Durocher
James Mak Gilbert - Software used for this entry:OptiStruct
- Patent status:none