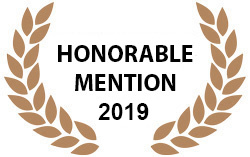
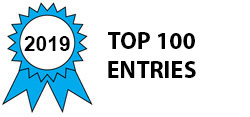
Electric vehicles in the form of cars, trucks and forklifts are becoming increasingly popular worldwide. The majority of these designs rely on a gear drive system to provide the correct ratio between motor RPM and wheel speed. The down side is that the torque from the motor damages the internal gears due to excess friction. In addition current designs require the electric motor to discontinue rotating while shifting from forward to reverse or when the vehicle is stopped. Continuous spooling of the motor from 0-15K RPM requires a large amount of energy and rapidly drains the battery pack.
These design defects are eliminated with the introduction of the continuously spinning magnetic transmission. The benefit of the constant spin feature is that a rotating motor creates a flywheel effect due to the centrifugal force. This force is converted into torque and reduces the amperage required to maintain the momentum of the vehicle.
The clutch assembly is composed of three separate disc plates. The center plate is composed of steel with a copper facing and is embedded with permanent magnets. This disc is attached to the input shaft of the motor. The two outer plates are composed of steel and permanent magnets and are are controlled by a paddle and shift rail. As one of the outer plates is moved closer to the center plate it begins to rotate in unison with the center plate and input shaft. The gap between the two plates is adjusted by the paddle. The magnetic force of the two plates induces them to rotate without making physical contact. The outer plates move in sync so that only one plate is in control of the center plate. The paddles simultaneously reduce the gap between one of the outer plates while increasing the gap of the opposite plate.
The left magnetic plate is connected to a belt drive which rotates the output shaft and produces a forward momentum of the vehicle. The right magnetic plate is connected to a spur gear and rotates the output shaft in the opposite direction to produces the reverse momentum. The motor is enabled to spin at a constant RPM at all times. The vehicle speed is adjusted using the gap between the two plates.
The benefits of this design include an increased battery run time, an extension of the battery life, a 60% increase in energy efficiencies and a longer travel range for electric cars and forklifts. The lack of contact between the plates eliminates the wear and tear that is typical of a gear based design. This magnetic transmission is light weight, scalable and manufacturing friendly. All of which contributes to a series of new products which are both viable and affordable
-
Awards
-
2019 Automotive/Transportation Honorable Mention
-
2019 Top 100 Entries
Like this entry?
-
About the Entrant
- Name:Earl Douglass
- Type of entry:individual
- Patent status:pending