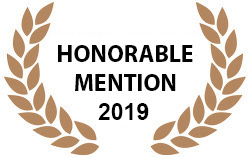
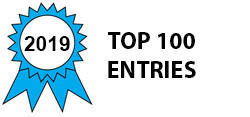
Ascend Manufacturing has invented the 3D printing technology of the future. Developed under a Nation Science Foundation grant and being perfected with world experts in 3D printing at Oak Ridge National Laboratory, our patent pending technology has so many industry disrupting advantages over existing technologies that puts us light years ahead of everything else on the market. Our technology, called Large Area Projection Sintering (LAPS), allows a user to create a single part or hundreds of thousands of parts in a single day all from a single low-cost machine. LAPS is the only 3D printing technology which fuses and forms a 3D part with an industrial closed loop control process – meaning every part has high repeatability and reliability.
Each part is sliced into individual layers and each layer is created sequentially on top of the previous layer to create a 3D part. LAPS utilizes an extremely high intensity projector (strong enough to burn a hole through wood) which projects images of each layer onto a bed of powdered plastic. Wherever the image strikes the bed, it melts and fuses an entire large area together, sometimes creating an entire layer all at once. Then, a new layer of powder is deposited and the process repeats until the full 3D part is created. Since large areas, or the entire layer in most cases is created simultaneously, this means that as this technology is scaled up, extremely large quantities of parts can be created without sacrificing overall print times. This also provides the ability to incorporate mature industrial processes which were previously impossible due to the physics of fusing small areas with other 3D printing processes.
What also makes this technology unique, is that multiple thermal and optical cameras watch the sintering (fusing) process, and updates the images which the projector is using. The thermal camera monitors and controls the temperature at each pixel ( ~25 microns in size) by measuring the temperature and making adjustments as necessary. This is what allows the full industrial closed-loop processing to occur and provides the ability to directly program sintering (fusing) temperatures rather than just laser powers or nozzle temperatures and scan speeds. Also, since multiple cameras are monitoring and controlling the process, the as-built parts can be directly compared to the input CAD file to confirm that every part reaches the required specifications (geometry and thermal profile). Large Area Projection Sintering can provide a post-build report of every part created with these verifications for certification purposes, requiring zero post processing quality assurance measures. Since this is a powder bed process, unsintered areas act as the support structure, meaning zero prost processing is required to remove any support material as well, making this the most rapid and agile manufacturing technology existing today.
Video
-
Awards
-
2019 Manufacturing/Robotics/Automation Honorable Mention
-
2019 Top 100 Entries
Like this entry?
-
About the Entrant
- Name:Justin Nussbaum
- Type of entry:individual
- Patent status:pending