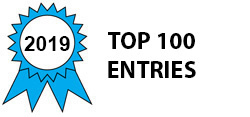
Traceability in plastic production is difficult, so we wanted to develop a general solution which did not cause any extra headaches.
We aim to place barcodes on injection molded plastic products of any size, color and geometry, without adding processes or requiring materials or contamination of the part. The barcodes should be scannable by in-line vision or scanners, to be generally useful.
We create the master structures for our barcodes through MEMS lithography, creating detailled diffraction gratings intermixed with smooth reflective areas. This way, our barcodes achieve both diffusion and diffraction properties, creating very high optical contrast between microstructured and reflective areas.
The master structures are imprinted in a sol-gel material directly on steel parts, which is then sintered in such a way that it maintains the microstructure after processing. The outcome is hard microstructured amorphous quartz, which is durable enough to withstand injection molding conditions.
We have made various trials molding different kinds of polymer, including most common types - in general, the microstructures transfer well to the plastic materials under normal (cold mold) molding conditions. Even thermoplastic elastomers perform well! The barcodes can generally be scanned, even by smartphone, when using the right scan software and taking proper care of lighting. Larger barcodes and darker polymers are easier to scan, but even a 3 mm x 3 mm barcode on white plastic could be scanned by smartphone, which is not possible when barcodes are laser-etched in the mold surface.
We have made a few trials with potential users. A medical device manufacturer considers implementation to ensure that no mistakes or mix-ups will occur during assembly.
Generally, placing machine-readable information directly on the plastic part solves and supports many of the challenges in the modern factory. Traceability can now extend all the way back to the molding process. Assembly becomes robust. Multi-tier supplier networks become transparent. Sorting and compartmentalization reduces impact of problems. Automated processes for quality control are simplified. Problem solving becomes fast and accurate. Compliance with regulatory demands improves. Anti-counterfeit measures become stronger.
Our microbarcodes will be ordered by the Customer for implementation in many molds. Customer only needs to specify content and size, then we provide the barcodes on steel material, for working into inserts to be placed anywhere in the mold cavity.
We want to help manufacturers put critical information directly on the plastic part! Small and large, - any polymer, any color, machine-readable barcodes providing strong traceability.
-
Awards
-
2019 Top 100 Entries
Like this entry?
-
About the Entrant
- Name:Guggi Kofod
- Type of entry:teamTeam members:Jan Kafka, Nastasia Okulova (Inmold A/S, Denmark), Dan Kofoed (SiOx Aps, Denmark), Guggi Kofod (Rel8 Aps, Denmark)
- Patent status:patented