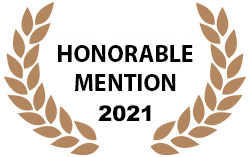
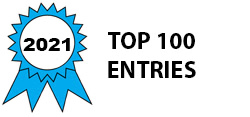
Our team has over many years developed a double acting fickett-jacobs cycle internal detonation engine that boasts pure isochoric constant volume heat addition, giving it the world's highest efficiency for a given stroke to bore ratio. Instead of conventional engine architecture, we have modernized the scotch yoke with new technology. Our working prototypes have a static compression ratio of 30 to one and our newer designs have a compression ratio of 300 to one, meaning we have the highest compression ratio engine ever made. The merits of such a design include but are not limited to the near total elimination of piston side thrust, pure sinusoidal reciprocating mass which obviates the need for counterweights in 4 and 8 cylinder designs, and the ability to use both sides of the piston as a combustion chamber for maximum power to weight ratio.
Our prototypes have achieved a power to weight ratio of 4 horsepower per pound and our double acting design has a projected power to weight ratio exceeding 8 hp/lbs. Our engine design is as simple as it is elegant with only two moving parts, allowing for fast, easy, and affordable mass manufacture and maintenance. This will facilitate a more rapid industrialization of developing nations, especially given the engines fuel agnostic capability of using unrefined biomass derived fuels and low grade fuels absent additives without compromise of low emissions or efficiency. Measured EGT's right out of the exhaust ports are 220 F under load. We have achieved reliable HCCI under all operating conditions without the need for complex monitoring and adjustment systems/algorithms because we exploit the elegance of physics rather than relying on over engineered systems.
With a measured BSFC of 0.25 and a calculated BSFC of future designs at 0.21, our 49cc design with its ability to produce over 60 horsepower is highly suitable for package delivery via drone because its vastly superior range and reliability will allow for a point to point model of parcel delivery for faster and more affordable logistics and will allow for multiple packages to be delivered with a total payload capacity upward of 75 pounds. The design allows for uninterrupted operation even in the event of total electrical system failure irrespective of cause. Another unique feature of this design is its ability to operate in lean burn conditions, which allows the engine to operate at its maximum volumetric efficiency throughout the entire RPM band (idle can be set as low as 100 RPM and can safely spool up to 30,000 RPM) by obviating the throttle plate from the design which virtually eliminates parasitic pumping losses caused by conventional throttle plates. This allows the engine to dynamically adjust the AFR to facilitate a load based fuel consumption irrespective of RPM, which means the engines torque can arbitrarily spike at any RPM by enrichening the mixture until stoich is reached. Lifespan is projected to exceed 100 thousand hours (approximately 10,000,000 miles) with modern metallurgy, coatings, and nano-tribological technology. There are many more advantages than this.
Video
-
Awards
-
2021 Automotive/Transportation Honorable Mention
-
2021 Top 100 Entries
Like this entry?
-
About the Entrant
- Name:Sky Huddleston
- Type of entry:teamTeam members:Sky Huddleston, Roger Richard.
- Software used for this entry:Fusion 360, Draftsight, FreeCAD
- Patent status:pending