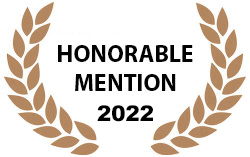
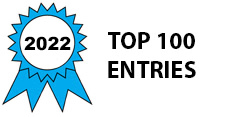
Coatings with a pseudo-alloy structure are a separate type of composite coatings. They consist of materials that do not form solid solutions and compounds in the liquid and solid states (differing in melting temperatures and not fusing with each other). Owing to the absence of interaction between these materials in a wide range of concentrations and temperatures, the pseudoalloy coatings combine the properties of each of their components. In the process of deposition of a multi-component coating particles of each of the deposited metals are preserved individually in a layer, although during arc spraying they were in the molten state. Such multi-component coatings are called the pseudoalloy ones. Materials of the type of pseudoalloys are characterized by a number of important properties, such as a combination of high values of melting and evaporation temperatures with mechanical strength, hardness, damping ability, wear resistance, self-lubrication ability under dry friction conditions, and a high level of electrical and thermal conductivity. The required properties of pseudoalloys are achieved by varying the ratio of their components.
Electric arc spraying allows producing pseudoalloy coatings from non-fusing metals with the required properties and a wide range of combinations of their components. This technology can provide the pseudoalloy coatings by using the alloy-forming components. A short time of contact of particles of the components (milliseconds) prevents development of the interaction processes.
On the basis of the requirements specified to protective coatings of molds, the materials of pseudoalloys were determined for applying coatings from two wires. One of the wires is copper, which provides maintaining a sufficient thermal conductivity of the layer, and the second one consists of a material, which provides wear resistance of a coating. As a second wire, the wires NiCr, Mo, Ti and a flux-cored wire were used, consisting of a steel sheath and a filler – FeB powder. Applying electric-arc spraying, the pseudoalloy coatings with a uniform distribution of components were produced, one of which is copper with a hardness of 1320-1460 MPa, and the second one is the strengthening component NiCr, with a hardness of 2440 MPa; Mo, with a hardness of 5350 MPa; Ti, with a hardness of 7540 MPa; FeB, with a hardness of 7050 MPa.
As a result of measurements of the coefficient of thermal expansion of coatings, it was found that the coating Cu-NiCr is the most close to the coefficient of thermal expansion of copper. Then it is followed by Cu-FCW (FeB), Cu-Ti and Cu-Mo. The resistance of pseudoalloy coatings to abrasive wear at a room temperature exceeds pure copper by 1.4-2.3 times. The tests of pseudoalloy coatings on resistance to wear during heating to 350 °C showed, that the wear resistance of Cu-NiCr and Cu-FCW (FeB) coatings exceeds the resistance of pure copper by 4.5 and 22 times, respectively. The hot hardness of the coating Cu-NiCr in the range of 20-400 °C exceeds the hardness of pure copper by 3 times.
-
Awards
-
2022 Manufacturing/Robotics/Automation Honorable Mention
-
2022 Top 100 Entries
Like this entry?
-
About the Entrant
- Name:Nataliia Vigilianska
- Type of entry:teamTeam members:Burlachenko Oleksii
Grishchenko Oleksandr - Patent status:patented