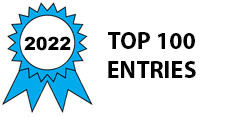
Space Engine Systems Inc. (SES), headquartered in Edmonton, Canada, is currently building the HELLO-1 Experimental, a Mach 5 Hypersonic vehicle using Air Breathing Turbo-Ramjet engines. The vehicle is undergoing full scale ground testing in preparation for flight testing this year.
The biggest challenge to success in hypersonic flight, for both commerce and defence, is heat. The World’s first Full Scale Heated Wing Up Bending Testing of the entire vehicle is being prepared. It will exceed the hypersonic mission design profile loads by 135 % under full heated condition and 150 % at ambient condition with a ramp rate from 30 to 60 seconds. The cockpit will be pressurized during the testing, adding to the severe loads. The HAF test facility is a mobile test platform in critical areas. It will operate from ambient temperature up to 1,400 deg Celsius using heated air generated by modified single and multiple jet engines. It can move 80 kg/second of heated air or multiples of this as required while bending under full load. The vehicle can be pulled out, cooled, and subjected to heat quickly by moving it back into the HAF facility. This will allow for cyclic load testing. NDT is done at the HAF facility upon completion of full load testing. The HAF mobile testing may be offered to other companies for hypersonic and other structural bending under heated conditions, matching various mission profiles.
The HELLO-1 X is 60 feet long and the air frame will be enclosed within the chamber subjecting the complete airframe to heat, simulating flight conditions. This will validate the structural thermal effects from the fluid thermal structure CFD modeling. The thermal gradient of the entire frame behaves differently. Coupled with bending we closely simulate full scale flight conditions reliably. The windshield’s capability to handle temperature without any failure and to cool down and test for cracks on the skin. We will observe the complete aerothermoelastic test of the skin during this test process. We will also determine the life of avionics and hydraulic systems in typical flight conditions during this testing. The DASS GNX turbo-Ramjet engines are fueled by hydrogen for net zero environmental impact.
Due to the very high specific impulse (Isp) of air breathing engines we are certain we can go to suborbital and LEO at a fraction of the cost compared to rockets. The HELLO-1 and HELLO-2 space vehicles will be moving towards manufacturing shortly thereafter. All SES vehicles are 100 % reusable, that take off like any plane and land like as a conventional aircraft from any airports around the world. It is simple, affordable and will rapidly become a mature technology with extreme reliability for space exploration, point to point and suborbital.
Video
-
Awards
-
2022 Top 100 Entries
Like this entry?
-
About the Entrant
- Name:Pradeep Dass
- Type of entry:teamTeam members:Pradeep Dass-Mechanical Engineer, President & CTO
Dan Handford-Ph.D(Mechanical)
Graeme Schmidt-Ph.D(Aerospace Engineering)
Joel Gagnon-M.Sc. in Aerospace Engineering
David Cerantola-Ph.Din Aerospace Engineering
James Seiffiedine–Mechanical Engineer
Lochlin. K. Mechanical Engineer - Patent status:pending