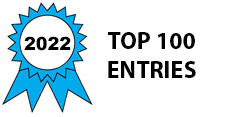
Founded in 2018, the company has created a new way of building composite parts, one that combines 3D printing technique and filament with continuous carbon fiber reinforcement and compression molding to create strong, light components. The multi-step method delivers parts that can be both cheaper and less wasteful than either conventional composite or machined parts, with less porosity and more repeatability than other continuous carbon fiber 3D printing solutions can provide.
9T Labs’ Red Series system consists of its Fibrify software and two different machines, the Build module and the Fusion module. The Build module is essentially a 3D printer with two deposition feet to place thermoplastic filament alongside continuous fiber-reinforced filament. The platform is open source, and customers are free to use whatever filament they wish with some adjustment to print parameters to maintain the proper temperatures. The continuous fiber is also off-the-shelf, but with some modification. 9T Labs sources continuous fiber tape and has it cut into 1-mm widths and respooled; this flat tape is fed into the Build module before being delivered to the print head in the build chamber.
The printhead itself features two deposition feet to apply the thermoplastic and continuous fiber filament selectively. Importantly, the reinforced filament need not follow the same path as the neat plastic; instead, this capability can be turned on and off as needed. The Fibrify software provides user-adjustable intelligent fiber layup suggestions and integrates with commercially available FEA simulation packages to verify and optimize these patterns. It is about placing the least amount of fiber for the maximum performance requested in order to be cost-competitive with metals.
Parts are usable right out of the printer as functional prototypes, jigs and fixtures, or one-off parts, but voids and dimensional accuracy preclude them from most of the high-performance production applications 9T Labs is truly after. To achieve their final density and dimensions, these “preform” parts go through a compression molding step in the Fusion module, capable of reaching temperatures up to 400°C and active pressure regulation of greater than 20 bar.
This step uses a mold tool unique to the part — typically machined aluminum for a short-run job, or stainless steel for higher volumes — to compress the printed layers and fiber together, resulting in a low-porosity, dense and strong final composite piece. Parts achieve less than 1% void content through the Fusion process. As an added benefit, bushings, bearings and other inserts can be added to parts before compression molding and secured into place during this step, reducing assembly on the other side. The process also allows multiple sub-parts to be assembled and fused into one part with a complex fiber orientation as well as preform reshaping in order to create parts with out-of-plane fiber orientation.
This technology targets the production of serial parts in markets including aerospace, medical, leisure & luxury, sports, general industry, automotive.
Video
-
Awards
-
2022 Top 100 Entries
Like this entry?
-
About the Entrant
- Name:Yannick Willemin
- Type of entry:teamTeam members:Martin Eichenhofer, Chester Houwink, Giovanni Cavolina, Fleurine Eberle, Yannick Willemin
- Software used for this entry:Ansys
- Patent status:patented