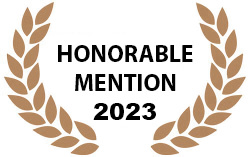

It is often desirable to deliver extremely high power laser output by fiber optics rather than free space, e.g., for surgical, welding, spectroscopy, yet coupling very high optical intensity into even ‘larger silica core’ fiber is replete with challenges. Laser damage thresholds for silica core optical fiber vary within the published literature but the bulk of failures are attributable to contamination, internal fiber stresses, surface flaws, and subsurface defects: artifacts of mechanical polishing. Mechanical polishing employs sequentially finer abrasive grits under controlled speeds and pressures at formulaic intervals to minimize imbedded particles and differential pressure induce subsurface flaws. It’s labor intensive, involves subjective operator judgement and cannot achieve 100% reliability. Mechanical polishing replaces large flaws with successively smaller flaws; regardless of the care taken, some size of flaws will always be present. Safe delivery of higher optical intensities necessitated the development of a defect-free fiber polish or a means of nondestructive testing (or inspection) capable of predicting fiber reliability.
At the request of a colleague in 2004, my company, InnovaQuartz® LLC (Phoenix, AZ USA), developed the basics of non-contact laser polishing for bare optical fiber. The technique had limitations of its own but did provide a one step and reproducible fiber surface for more than a ten-fold improvement in laser damage threshold versus the best mechanical polish. Over the past two decades, much higher laser pulse energies have been produced in shorter pulse widths. Coupled with a trend towards using smaller fibers for accessing remote targets, often by way of highly tortuous routes, e.g., endoscopic management of bile duct stones, applications for fiber delivery of ridiculously high optical intensities have emerged.
While fiber burn through is unacceptable in most applications, disposable surgical devices must be safe, effective, sterile, and available at low cost. The ProFlex Prometheus™ laser launch termination satisfies all these needs with a failure probability of 1/10,000 at double the maximum bending stress of surgical use. The input is tolerant of misalignment, beam blooming and drift, and resists abrasive damage. The concave input surface serves to partially collimate the laser focus within the ‘jump taper’ for lower mode fill and with the consequent reduction in divergence, a 4-fold higher radiant intensity is delivered to the target. The one piece fiber construction lowers production costs while eliminating splices. A 200 micron core fiber safely couples to large and unstable multimode laser foci to safely deliver terawatts per square centimeter pulses.
Such optical intensities may reliably ignite rocket motors for better assurance of simultaneous ignition in vehicles like SpaceX’ Starship or for reliable pilot ejection in igniting jet fighter cockpit explosive bolts. In situ spectroscopy is augmented for applications like pollutant monitoring deep within aquifer and myriad industrial uses are imagined. For reference, routine lasering kidney stones involves hundreds to thousands of pulses at tens of megawatts per square centimeter.
-
Awards
-
2023 Aerospace & Defense Honorable Mention
-
2023 Top 100 Entries
Like this entry?
-
About the Entrant
- Name:Stephen Griffin
- Type of entry:individual
- Software used for this entry:Solidworks
- Patent status:pending