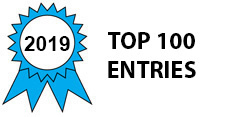
With water shortages on the rise, wastewater is a looming concern that leaves the world’s top minds in a constant battle to combat the inefficiency and high cost of water treatment and disposal. Most industries produce wastewater. Over 80% worldwide, and 69% in the U.S., of industry’s wastewater is not reused; posing massive issues with treatment, disposal, and environmental impact. Industry’s current response to increased regulation and wastewater treatment costs is to move to a Zero Liquid Discharge (ZLD) solution, using a variety of very expensive treatment processes to concentrate the effluent. The ZLD market alone is growing to $8.1 billion by 2025.
The cheese industry is moving toward ZLD, with its 5.3 billion pounds of brine producing Italian cheese processed each day. Micronic has secured a cheese customer that produces 80 million pounds of cheese per day along with 100,000 gallons of brine per day that will be reused, after processing through Micronic’s water concentration technology, MicroEVAP™.
MicroEVAP™'s 3rd-party testing has validated removal of ultra-high total dissolved solids (TDS), suspended solids, bacteria, metals, E. coli, pharmaceuticals, nitrates, and nanowaste. MicroEVAP™is a closed-loop patented mechanical evaporation system that reclaims air and heat and is powered by a blower. It includes a stationary and patented geometry (or ‘pod’) that creates a vortex inducing evaporation, at low temperature and pressure, separating contaminants from water in a single step. Water micro-droplets are created; a small amount of which carries out solids leaving >95% of the feedwater for efficient evaporation and re-capture as clean water through condensation. Less than 5% highly concentrated and high-value brine remains for resource recovery. Trials of the current pilot reduced salts by 99.2% to 99.98%, with demonstrated throughput between 90.3% and 98.3%; both critical to the ZLD market Micronic is pursuing.
Independent competitive analysis has projected our food grade system costs at 15% CAPEX and 33% OPEX of the competition. MicroEVAP™’s smaller footprint and the single step process, that reduces multiple now obsolete steps, contribute to significantly reduced CAPEX. Turbulent flow (vs. laminar) inhibiting scale production; the fact that MicroEVAP™ uses no chemicals, filters, or membranes; and reduced energy consumption make the system low OPEX.
While MicroEVAP™ is novel and embracing the tornadic activity as new to the engineering body of knowledge; the unit itself is not complex to manufacture. Most of the components are commercially available, e.g., motor, blower, intercooler, materials, piping, etc., and will be purchased for fabrication and assembly by contract manufacturers. Micronic will take delivery and conduct full scale testing on systems before final customer delivery.
We believe that, for several water reuse markets, MicroEVAP™ is the only technology that eliminates the significant capital and operational expenses necessary to embrace and achieve absolute ZLD. Competitors cannot address this need either because it is too hard, or they won’t because it’s too expensive. MicroEVAP™ closes this severe market gap. MicroEVAP™ allows industries to reuse >95% of their water that collectively will reduce pollution, enhance access to clean water, and significantly reduce costs.
-
Awards
-
2019 Top 100 Entries
Like this entry?
-
About the Entrant
- Name:Karen Sorber
- Type of entry:individual
- Patent status:patented