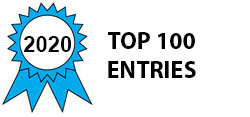
Concentrated heat loads i.e., very high heat fluxes from electronic components present significant thermal management challenges in defense, space, and commercial applications. Such high heat fluxes increase the temperature of components beyond permissible operational limits. These high-temperature zones are often referred to as hotspots and deteriorate system performance and reliability as conventional passive heat sinks are not able to tackle hotspots (I, Illustration 1). Accordingly, heat spreaders are required that can quickly spread heat from the smaller hotspot area, a to a larger sink area, A (II, Illustration 1).
In this regard, liquid-vapor phase-change based passive heat spreaders promise efficient heat dissipation due to high latent heat of vaporization of coolant liquid. These devices are sandwiched between electronic component and heat sink to address the hotspots (III, Illustration 1). Heat is absorbed from the hotspot of smaller area (a) through evaporation/boiling of pure coolant liquid, and the resulting vapor travels to heat sink of larger area (A) due to pressure difference/buoyancy. The heat sink, which is maintained at relatively lower temperature, allows condensation of incoming vapor. The condensed liquid is recirculated to evaporator end via capillary-action/gravity.
Thermal performance of these devices is significantly dependent on component/evaporator mounting. When evaporator is mounted on top (-1g), essentially wicks are required in between evaporator and condenser of heat spreader to return condensed liquid to evaporator. Incorporation of wicks increases device complexity and cost. Moreover, the flow of liquid through wicks is susceptible to blockage over prolonged usage, primarily due to corrosion and generation of non-condensable gases. Alternatively, wickless heat spreaders fail in such conditions, where gravity does not assist vapor removal and also does not allow condensed liquid to return evaporator end.
To address these issues, we designed, developed, and tested a novel passive wickless two-phase heat spreader wherein instead of pure coolant liquid, an aqueous solution of surface-active ionic liquid (SAIL, [BMIM][OS]) as a coolant is completely filled in the heat spreader (Illustration 2, top right image). Unlike typical two-phase devices available in the market, our device is very simple, easy to fabricate and does not rely on gravity or wicks for coolant recirculation. The force of repulsion due to interaction of SAILs adsorbed at liquid-vapor interfaces of thin-liquid films contained between neighboring bubbles (Illustration 2, bottom right image) nucleating at hotspots is strong enough to cause bubble departure at all orientations. Uniform temperature distribution on the heat sink end acquired from the infrared camera suggests that these non-coalescing bubbles quickly spread over larger area and condense to release heat to sink (Illustration 2, bottom left image). This passive mechanism of heat dissipation demonstrates orientation independent performance and can tackle hotspots heat flux of > 1 MW/m2 within a temperature budget of ≈ 25 °C.
Very high cooling capability independent of component orientation and gravity along with simple design and manufacturing, low cost, and fast response of this device makes it a suitable alternative of complex wicked and less reliable heat spreaders for effective thermal management of earth and space electronic devices.
Video
-
Awards
-
2020 Top 100 Entries
Like this entry?
-
About the Entrant
- Name:Nirbhay Kumar
- Type of entry:teamTeam members:Nirbhay Kumar, Graduate Student
Dr. Rishi Raj, Associate Professor
Department of Mechanical Engineering,
Indian Institute of Technology Patna, India - Software used for this entry:Comsol Multiphysics
- Patent status:patented