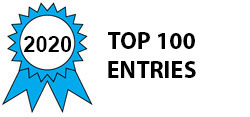
A January 2016 report from the World Economic Forum projected plastics production, which was 311 million tons in 2014, will double by 2034. Production of ethylene, the basic building block for these materials, represents the single most energy-consuming process in the chemical industry.
LoTempLene has the potential to modernize these industrial processes and scale back their energy consumption. The process could reduce emissions from ethylene production up to 98 percent when driven by energy from carbon-free sources such as solar, wind, or hydropower. By capturing hydrogen and putting it to use in fuel cells, LoTempLene offers a net gain in process energy.
There is no industrial process that consumes energy more voraciously than petrochemical manufacturing. Since the early 20th century, everything from gasoline and diesel fuel to plastics has been made by cracking complex hydrocarbon molecules found in oil and coal with tremendous amounts of heat and pressure.
One of the petrochemical industry’s primary building blocks, ethylene, is used to make polymers and their derivatives. Worldwide production of ethylene reached more than 143 million tons annually in 2012, according to Oil & Gas Journal. Ethylene production represents the single most energy-consuming process in the chemical industry, according to the Department of Energy’s Energy Information Administration.
Now, the American shale gas boom has opened up new possibilities for the nation’s petrochemical manufacturers. Ethane, a major component of natural gas liquids, offers a simpler hydrocarbon to refine than oil. Once it is converted to ethylene, it becomes a primary building block for products ranging from polymers and plastics to antifreeze and adhesives.
For decades, ethane has been converted to ethylene the same way oil is processed, with industrial steam cracking at temperatures as high as 850 C. But a team of INL researchers wanted to find a less energy-intensive approach that could make use of abundant domestic natural gas resources.
That team pioneered an innovative electrochemical process called LoTempLene, which uses far less energy and emits less carbon dioxide than steam cracking. By using an electrochemical cell to convert the ethane in natural gas to ethylene, LoTempLene creates more of this petrochemical building block while generating pure hydrogen in the process. The declining cost of electricity now makes electrochemical refining more economically feasible. If the LoTempLene process were powered by a renewable source and the captured hydrogen were to be incorporated into fuel cells, there would be a net gain in process energy.
The technology could fundamentally change the petrochemical manufacturing paradigm from fossil-energy-fueled “thermal” practices to a clean energy approach that uses the nation’s vast natural gas resources while incorporating renewables such as wind and solar.
-
Awards
-
2020 Top 100 Entries
Like this entry?
-
About the Entrant
- Name:Andrew Rankin
- Type of entry:teamTeam members:Dong Ding, Wei Wu, Ting He, Lucun Wang
- Patent status:pending