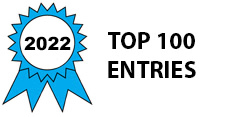
Researchers at INL have developed a large-scale spark plasma sintering process. While small scale SPS has been accomplished, the novelty of this process lies in the tooling and knowledge developed to address the scale up issues and fabricate a viable armor tile. This process utilizes a graphite material that has minimal thermal expansion characteristics to reduce the susceptibility to cracking under high mechanical stress. To minimize the pressures required to press out the product from the dies, a novel axial profile was developed in which a tapered wall alleviates contact easing the process of press out. At high current densities, silicon carbide decomposes and forms a silicon-rich liquid. This liquid can be utilized for an in-situ sintering process that can produce high density material.
Because of the in-situ Si-liquid generation observed in the silicon carbide, the SPS process enables fabrication of dense material at low pressures. This means that manufacturing curved and more complex shapes becomes feasible. Additionally, due to its application of the electrical energy directly to the sample and die, SPS is more energy efficient than traditional furnaces. The SPS process also makes material that is harder than that produced by other methods. This process is significantly faster and has the potential to create lower-cost products on the mass scale. The results are time and money savings.
The immediate use for this process is the production of high-quality armor tiles. However, there could be other potential applications with additional research. Any field which needs dense silicon carbide products, especially those with complex configurations, may have use for this technology.
-
Awards
-
2022 Top 100 Entries
Like this entry?
-
About the Entrant
- Name:Andrew Rankin
- Type of entry:teamTeam members:Michael Bakas and Henry Chu
- Patent status:patented